光伏产业链的上游是晶体硅原料的采集和硅棒、硅锭、硅片的加工制作,产业链的中游是光伏电池和光伏电池组件的制作,目前晶硅电池分为单晶硅和多晶硅两种,产业链的下游是光伏电站系统的集成和运营,如下图所示。
图1. 光伏行业产业链
数据来源:互联网公开资料
从技术上来看,光伏产业链上游涉及的技术有多晶硅制备工艺、单晶硅拉棒技术、多晶铸锭技术和晶硅切片技术。产业链中游涉及的技术有电池技术。产业链下游涉及的技术有光伏电站并网技术、光伏电站发电性能评估技术和光伏智能化数据平台技术。
光伏产业链的上游包括晶体硅原料和硅片。作为产业链的最上游的晶硅制造,目前这个环节的技术要求很高,具有一定的技术壁垒和垄断性。目前制备多晶硅的工艺技术主要有改良西门子法,硅烷法和冶金法三类。
改良西门子法是在西门子法的基础上增加了尾气回收和四氯化硅氢化工艺,实现了生产过程的闭路循环,既可以避免剧毒副产品直接排放污染环境,又实现了原料的循环利用、大大降低了生产成本(针对单次转化率低),如下图所示。
图2. 改良西门子法生产工艺流程:
资料来源:互联网公开资料
硅烷法是指利用高纯度硅烷在反应器中热分解为高纯度硅。硅烷法可以分为两类,较早出现的是硅烷西门子法(Silane Siemens),即用硅烷(SiH4)而非TCS作为CVD还原炉的原料,通过硅烷的热分解和气相沉积来生产高纯度多晶硅棒料,REC旗下的REC Silicon公司采用过此方法生产电子级多晶硅;
后来出现了另一类方法——硅烷流化床法(Silane FBR),以STC、H2、冶金硅和HCI为原料在流化床(FBR)高温(500℃以上,不算很高)高压(20bar以上)下氢化生成TCS,TCS通过一系列歧化反应后制得硅烷气,将硅烷气通入加有小颗粒硅粉的流化床(FBR)反应炉内进行连续热分解反应,生成粒状多晶硅。
在三种生产工艺中,改良西门子法为目前的主流方法,根据ITRPV的预计,由于成本控制的潜力因素,未来硅烷流化床法将逐步取代改良西门子法的份额,在2025年旗鼓相当,共同成为主流的制备方法,如下图所示。
图3. 硅烷流化床法生产工艺流程
数据来源:互联网公开资料
硅片制造是晶硅制造的下一个环节,也属于整个产业链的上游层面。与晶硅制造环节不同,该环节为资本密集型,技术含量不高,产品工艺与投入设备相关,可分为单晶硅片和多晶硅片。
硅片成本中,多晶硅成本占比较高,且多晶硅价格变动较为频繁,因此成本核算中,将硅片成本分为硅成本和非硅成本。而单晶和多晶的成本差别主要体现在拉棒和铸锭成本的差别上,一直以来,多晶对于单晶的成本优势建立在铸锭相对于拉棒更高的效率上。
切片环节单多晶的切片成本大致相似,与选择的切割方式有关,金刚线切片的成本低于砂浆切片,而单晶的金刚线切片成本略低于多晶金刚线切片。目前,单晶切片基本已经普及金刚线切片,多晶正由砂浆切片向金刚线切片过渡,且速度非常快。
目前在光伏市场上,太阳能电池主要是晶硅类产品,也有小部分薄膜类产品。晶硅电池包括单晶硅和多晶硅两类。从电池转换效率来看,常规多晶量产转换效率在18.8%,结合黑硅技术效率约19.2%。
常规单晶效率在20-20.2%,而PERC单晶组件相比常规组件,每瓦发电量高出2.5%-3%,高发电量主要得益于弱光性能好、功率温度系数低、工作温度低等等,当然还有低衰减。因此在系统成本方面,可以节省电缆、支撑结构、逆变器、安装以及土地成本,最后给用户带来高收益。
成本降低与技术进步,使得单晶性价比优势显著。目前,我国单晶电池比多晶电池的转换效率平均高2%左右。而即使完成金刚线和黑硅改造,多晶成本优势依旧不明显。随着拉晶成本逐步降低,单晶高性价比凸显。
硅片价格大趋势下行,短期内供需的错配导致波动出现,长期趋势取决于成本下降。2016年以来,单多晶价差有拉大的趋势,一方面反映了单多晶不同程度的供需情况,另一方面也是由于单晶路线下游电池和组件端的高效化进展神速。
未来单晶电池比多晶电池具有更大的效率提升空间和更快的实现速度,效率差距将进一步扩大。
因此,单晶技术路线通过提升效率降低光伏发电成本的过程中占据更大市场份额,如下图所示。
图4. 光伏晶硅电池中单多晶市场份额对比
数据来源:CPIA
最后,薄膜电池一般是在玻璃、不锈钢等物质表面附上几微米厚的感光材料制成。
主要优势有:
(1)薄膜电池使用原材料少、制造工艺简单、耗能少、可大面积连续生产,并可采用玻璃或不锈钢等低成本材料作为衬底。
(2)可制成能弯曲的柔性产品,应用范围广。
(3)弱光性好,在辐照度较低的情况下也会有功率输出。
主要劣势有:
(1)薄膜电池的光电转化率偏低,转化效率最高的铜锢硒量产效率也只能达到15%,硅基薄膜电池更是量产效率在10%以下。
(2)薄膜电池的设备和技术投资是晶硅电池的数倍。
来源:中衍资讯
END
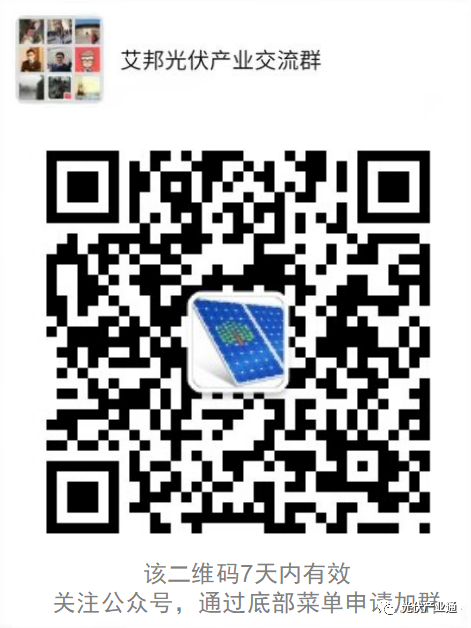
推荐阅读:
原文始发于微信公众号(光伏产业通):从晶硅电池到薄膜电池:光伏电池工艺概况
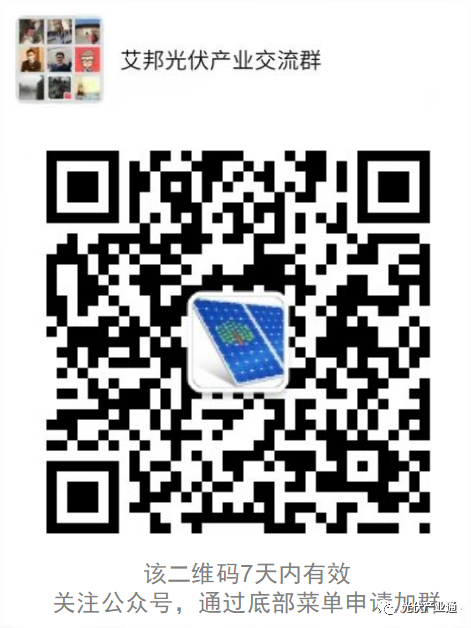