为进一步降低风电叶片重量及成本,提高竞争力,整个风电行业加速了对新材料或新技术的开发和应用。通过采用力学性能更优的增强纤维,如用高模玻璃纤维或碳纤维,可明显提高复合材料的力学性能,但同时也带来了更高的成本。
而通过采用更先进的复合材料制造工艺可充分发挥增强材料的力学性能,实现叶片减重和降本的目的。
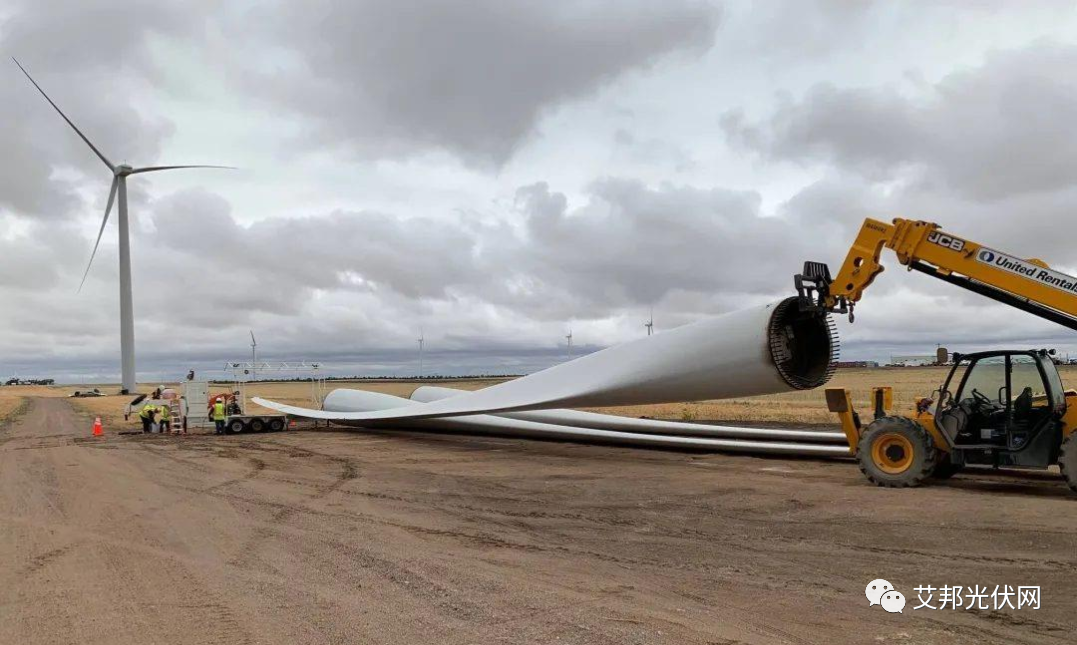
拉挤成型技术始于20世纪50年代,至80年代已发展成为纤维增强复合材料的主要成型方法之一。
近年来,拉挤成型技术更是受到各行业的重视,其产品向着形状复杂化、截面尺寸极端化、生产高效化、种类多样化、高性能化等方向发展,适用于各种工程领域。如从细到1mm的线材到70mm的棒材,再到800mm×280mm空腹型材,部分产品的拉挤速度高达6m/min。
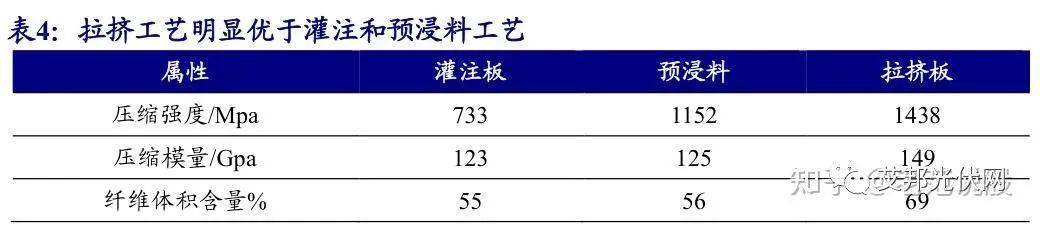
拉挤板是由多束增强纤维浸渍树脂后通过拉挤工艺制成的具有一定截面形状、连续长度的复合材料板材。拉挤工艺使纤维有一定的张力,能够显著提高制品沿纤维方向的力学性能,故其关键性能优于灌注织物和预浸料复合材料制品。
国际著名风电制造商Vestas公司率先采用拉挤板拼装主梁技术,将原本为一个整体的主梁部分拆分为拉挤板标准件,经组装成型。这一革命性创新设计极大地推动了拉挤板在风电叶片领域的应用。
本文介绍风电叶片主梁用拉挤板的发展历程、技术优势及应用现状,提出了拉挤板在未来风电叶片应用的发展方向。
20年前,欧洲采用手糊、真空灌注、预浸料方式生产风电叶片主梁,但一些关于碳纤维的制造缺陷难以避免。
2003年,Vestas率先申请了使用拉挤板来制造风电叶片主梁的专利。
2015年,Vestas把整体成型主梁拆解为高效、低成本、高质量的拉挤板标准件,实现组装并灌注成型。
通过大量测试验证及改进,Vestas率先全球在风机叶片上规模化使用碳纤维拉挤板。之后开发的2.0MW以上叶片均使用该产品,极大地推动了碳纤维拉挤板在风电领域的应用。
近几年,GE-LM、Siemens-Gemesea、Nordex等国外叶片厂商陆续突破Vestas专利限制,设计出各自的碳纤维拉挤板,并在大型叶片上应用。
以2021年为例,风电叶片中碳纤维用量为3.3万吨,主要应用形式为拉挤主梁。因此,拉挤成型工艺已成为风电叶片碳梁生产的主流工艺。
国内则是在获取玻纤拉挤板制造及应用的开发经验后,一部分整机厂、叶片企业、材料供应商转向开发碳纤维拉挤板,并逐渐应用到百米以上的海上大型风电叶片上,如上海电气的102、运达风电的110、金风科技的123等叶型。

碳纤维拉挤板开发初期使用国外碳纤维,随着国产碳纤维技术的进步及价格优势,逐渐成为国内碳纤维拉挤板的主要供应渠道。通过调整纤维与树脂之间的匹配,碳纤维拉挤板的模量可从130GPa提高至145GPa,进一步提升了叶片轻量化水平。
欧美曾经研究过使用玻纤拉挤板制造叶片主梁,如风力发电机制造商Senvion公司使用NEPTCO公司的RodPack拉挤板与UD织物混合灌注形成叶片主梁,但该方案一直未得到批量使用。近年来,欧洲有些叶片设计公司和制造公司陆续开发玻纤拉挤板,但目前仍未见应用案例的报道。
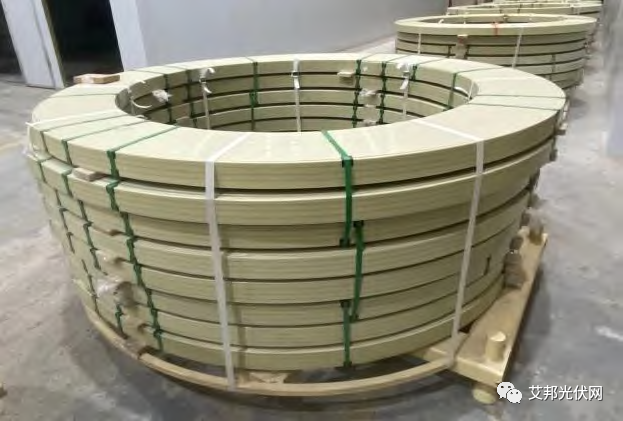
与国外开发拉挤板的顺序不同,国内首先开发并应用的是性价比更高的玻纤拉挤板。2014年,中复连众复合材料集团有限公司(简称中复连众)率先申请了拉挤板在风电叶片上应用的专利。

2019年,中复连众联合中复碳芯电缆科技有限公司(简称中复碳芯),成功突破了高强玻纤拉挤板制造及其在大型风电叶片上的一体化灌注等技术体系,开发了应用拉挤主梁的兆瓦级叶片。
随之,国内越来越多的整机厂、叶片企业、材料供应商投身于拉挤板及其应用技术研发,产生了大量专利技术,涉及到拉挤板截面、拉挤板制造工艺、拉挤板应用等方面。
国内拉挤板开发初期,行业先聚焦于低成本玻纤拉挤板及其应用技术研发,通过使用超高模玻纤(浸胶模量95GPa左右)和高树脂含量开发高性能的拉挤板。
掌握一定经验后,为实现叶片降本,采用低一级别的高模量纤维(浸胶模量90GPa左右)和低树脂含量,进一步提升玻纤刚度和强度转化效率,成功开发出性能相当的拉挤板。
整个国内市场快速积累并共享了制造及使用经验,由此拉挤板在大型风电叶片上得到广泛应用。
目前,一些企业利用超高模玻纤及低树脂含量,正试图开发更高性能的拉挤板,期望拉挤板设计模量达到65GPa-68GPa。
国内对多种体系的拉挤树脂,如不饱和聚酯、聚氨酯、环氧树脂等进行过研究,因环氧体系工艺成熟、性能高且稳定,成为目前行业内的主流体系。另外,国内企业突破了Vestas所定义的薄而宽片材截面概念设计,创新开发了窄而厚截面,大幅提升了拉挤板对叶片几何外形的普适性以及叶片主梁灌注质量。
目前碳纤维材料价格昂贵,其制造的拉挤板主梁成本高,只能用于百米级海上风电叶片。为了降低材料成本,同时又保留较高的性能。
国内叶片材料厂商将开发方向转向了碳玻混编拉挤技术。该技术结合了碳纤维高强高模、低密度与玻璃纤维高延伸率、低成本的特点,突破了传统玻璃纤维大叶片设计所面临的低模量,重量大的技术壁垒。
通过改变碳纱和玻纤的比例,可以实现模量由60Gpa到120Gpa的线性变化。为叶片设计、优化、减重、降本等提供了更多可能,为性能、重量与成本寻找到最佳契合点。

2021年7月,国内首款碳玻混主梁叶片-明阳智能MySE11-99A1叶片成功下线,该叶片长99米。目前,华美、风渡、中复碳芯等多家拉挤复合材料供应商为明阳提供碳玻混大梁产品,并已应用于多款叶型。

明阳智能MySE11-99A1叶片 图源:明阳智能
传统的拉挤板上下表面均附有一层脱模布,其主要作用为形成粗糙粘接面、吸收脱模剂及保护板材表面免受污染和损伤。
但脱模布的使用带来了材料、生产设备及质量控制成本的增加。
为此,自2022年以来,国内多家拉挤板厂商陆续研制免脱模布拉挤板,以提高其产品的竞争优势。
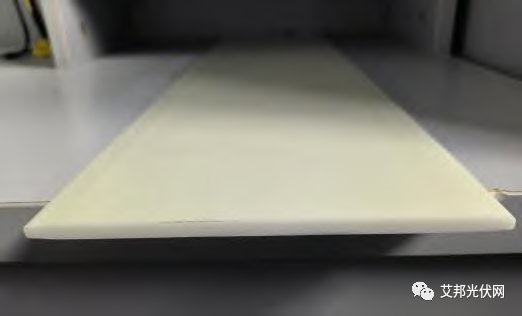
目前,三一已在多个叶型上批量使用免脱模布片材,并计划进一步扩大应用范围;中材、时代、重通和双瑞等均已进入试用或小批量阶段。
近两年来,环氧树脂价格上浮超过34%,造成叶片成本上涨超过10%。因此,迫切需要寻找一种低成本高性能的树脂替代环氧树脂。
聚氨酯树脂由于其低成本、高韧性及抗疲劳的优点,为叶片的降本及性能提升提供了新的思路。
另一方面,拉挤板的生产成本因素中,拉挤速度影响最大。而聚氨酯较环氧树脂粘度低且固化速度快,能够有效提高拉挤速度从而降低生产成本,与环氧体系相比,可以节约高达20%的生产成本。

2020年,中材叶片最早试用聚氨酯拉挤大梁。2023年2月,时代新材TMT95叶型的首支测试叶片采用了玻纤增强聚氨酯拉挤板大梁。
不过,由于该叶片尚未完成全尺寸测试验证,后续批产叶片仍采用环氧树脂体系的拉挤板。因此,目前行业内尚无聚氨酯拉挤大梁批量应用案例。
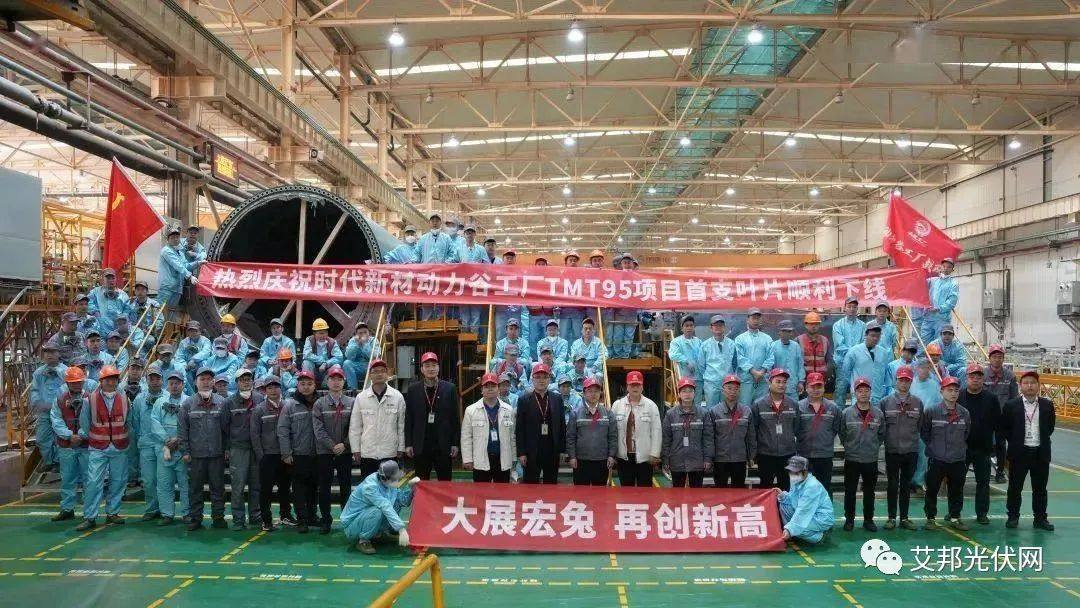
时代新材TMT95聚氨酯拉挤大梁叶片 图源:时代新材
拉挤工艺纤维体积含量高达70%,明显高于真空灌注(纤维体积含量范围55%-60%);而且拉挤工艺成就了更高的纤维直线度。两者结合大幅提升了纤维模量、强度转化到复合材料中的比例。
表1 各类单向复合材料的性能
从表1可以看出,玻纤拉挤板的模量可达62GPa,而传统的灌注玻纤布的模量仅能达到50GPa,前者模量较后者提高24%。比较单位质量复材的模量,玻纤拉挤板较灌注玻纤布高出约16%。
碳纤拉挤板的模量可以达到135GPa,而碳纤维预浸料的模量仅能达到125GPa左右,碳纤维拉挤板的模量较预浸料提高8%-16%。比较单位质量复材的模量,碳纤维拉挤板的模量较预浸料高出约7%。
以国内某84m叶片为例,玻纤拉挤板主梁叶片较灌注主梁叶片减重约500kg,减重约为2.5%;而碳纤维拉挤板叶片相比玻纤主梁叶片减重比例可达15%-30%。
稳定的拉挤工艺参数、生产环境、含胶量和纤维张力,使得复合材料内的纤维直线度始终保持在高水平,有效提升了产品质量和性能的稳定性。解决了真空灌注、预浸料成型工艺所带来的叶片主梁皱褶问题,减少了生产质量成本。
拉挤主梁模块化生产是将拉挤板卷材按照所需长度裁切、组装形成拉挤主梁,再吊入叶片壳体模具内,与壳体一体化灌注成型。此过程节省了不同型号叶片所需的主梁模具及其空间投资。统一的裁切组装工装可以柔性应对不同叶片型号需求,大量节省固定资产投资。
2019年,中国风电叶片自用拉挤板业务起步,经过3年的迅猛发展,目前国内主流叶型中,拉挤板主梁已基本取代了传统的玻纤真空灌注梁、碳纤预浸料梁。据最新统计,国内风电叶片主梁用拉挤板生产线总量高达1420余条,总产能预估36万吨,其中碳板产能预估1.8万吨。
目前,拉挤板已经形成了成熟稳定且规模化的供应链,国内风电叶片用拉挤板完全由国内市场提供,国外叶片厂商(如Vestas、GE-LM)也从国内大量采购拉挤板。
拉挤板在叶片主梁上已获得批量使用,但是在应用端仍面临诸多挑战。
例如:脱模布烘干不彻底影响环氧树脂的固化、搭接导致的质量缺陷及损耗、脱模布褶皱、撕除导致的脱模布残留以及撕伤板材本体。
随着追求高模量和高生产效率,纤维含量和拉挤速率的提高,会进一步增加拉挤板内应力,进而影响拉挤板的直线度及平面度,在大梁拼装使用中出现不随型或偏移等问题。
在拉挤板组装堆叠中可能会出现堆叠形成富树脂;灌注过程存留气泡或出现缺树脂情况等。
另外,拉挤主梁与壳体灌注成型,当出现灌注缺陷后,如何进行有效维修,以确保不影响叶片结构安全,也是行业内目前关注的一个重点问题。
(1)国外风电叶片用拉挤板目前仍只有碳纤维拉挤板;而国内拉挤板技术近两年内发展迅速且多样化,开发出了更具性价比的玻纤拉挤板、碳玻混拉挤板、免脱模布拉挤板和聚氨酯拉挤板,助力了国内风电叶片的大型化发展。
(2)拉挤板与传统的UD织物真空灌注、预浸料复合材料相比优势明显,具有更高的机械性能、更优的质量稳定性以及更低的生产投入成本。
(3)碳纤维拉挤板技术渐趋成熟并逐渐得到批量应用,随着海上风电的发展及碳丝国产化进程加速,碳纤维拉挤板将会有更广阔的的发展应用前景,同时也对其质量稳定性提出了更高的要求。
(4)玻纤拉挤板已在风电叶片行业内得到批量应用,因其低成本的巨大优势,在未来的陆上风电叶片中仍会占据主流,并将往更高模量、低成本的方向继续发展。
(5)在风电行业减重、降本、环保的大环境下,碳玻混拉挤板、免脱模布拉挤板及聚氨酯拉挤板应运而生,并在部分叶型上得到了批量应用或试用。
参考资料:风电叶片用拉挤板应用现状及发展趋势,徐强等,中复连众,中复碳芯。
原文始发于微信公众号(艾邦光伏网):风电叶片用拉挤板优势及应用现状
艾邦建有“光伏产业交流群”,群友有光伏电站、BIPV、光伏组件,电池片、背板,封装胶膜,接线盒、接插件、光伏边框、光伏支架、逆变器、光伏玻璃等零部件以及EVA、POE、PVDF、PPO、PA、硅PC、PET膜、氟材料、光伏银浆、焊带、粘接剂等材料以及相关生产、检测设备的上下游企业。欢迎扫码加入探讨。
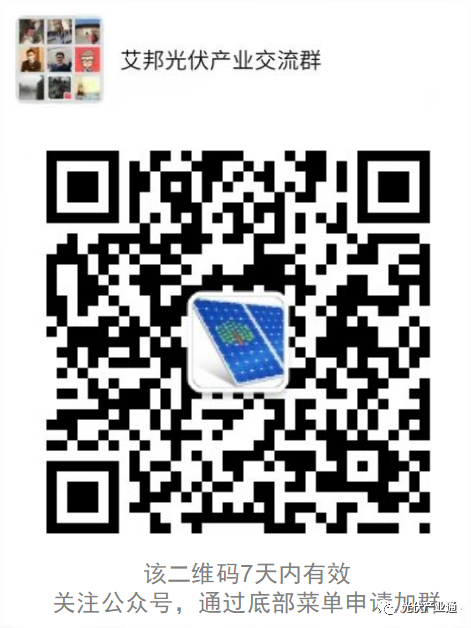
艾邦建有光伏边框、支架交流群,已有天合光能、晶科、亿晶光电、德毅隆、沃莱、博菲电气、爱康、振石、桐昆、福膜、云晟、恩贝斯、科思创、万华、立邦、百昊威等复合材料光伏边框、支架生产企业及拉挤设备、喷涂设备、聚氨酯树脂、玻纤、聚氨酯水性漆等产业上下游企业加入,欢迎扫码加入群聊!
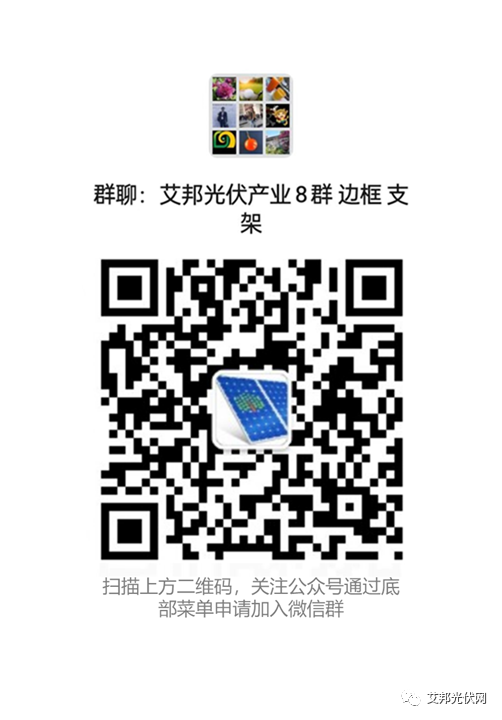