POE胶膜与EVA胶膜相比,具有更高的水汽阻隔率、耐候性能和更强的抗PID性能,其水汽透过率仅为EVA胶膜的1/8,可以有效降低PID效应,主要用于单晶PERC(发射极和背面钝化电池)双面、N型电池组件的封装。
EPE胶膜即“EVA-POE-EVA”三层复合结构膜,属于共挤型POE胶膜,既具备POE胶膜的高阻水性和高抗PID性能,也具备EVA胶膜的双玻组件高成品率的层压工艺特性,适用于PERC双面双玻、N型双面双玻以及其他耐候性要求较高的光伏组件的封装。
POE是采用茂金属催化剂的乙烯、丙烯和“-烯烃(1-丁烯、1-己烯、1-辛烯等)经过配位聚合得到的弹性材料,具有低密度、窄分子量分布等特点,兼具塑料和橡胶的双重特性,综合性能优异,主要被应用在塑料改性(增韧增柔)、汽车部件、光伏封胶膜和鞋材发泡等领域。
其中乙烯基弹性体为主,以乙烯为主要聚合单体,大多为乙烯与1-辛烯或者乙烯与1-丁烯的无规共聚产品,其乙烯含量(质量分数)58%~75%,乙烯与1-辛烯共聚物是目前POE材料中发展迅速的一类。
一般POE共聚单体含量高于20%,反之(共聚单体含量低于20%)共聚产物则为聚烯烃塑性体(POP)。
POE与POP之间没有本质的区别,只是共聚单体含量上有所不同,由此也引起二者密度有所差异,一般POP的密度(0.886~0.911g/cm3)高于POE的密度(0.857~0.885g/cm3)。
从两者的性质差异来看,POE具有良好的韧性、耐老化性、耐环境应力开裂性、电绝缘性等,适用于改性增韧聚丙烯(PP)、聚乙烯(PE)和尼龙(PA)以及生产电线电缆、汽车零部件、光伏胶膜等,还可以与EVA材料共混发泡制作鞋底材料、汽车坐垫、鼠标垫、箱包里衬等。
POP具有低起封温度、高热粘度、抗污染热封、抗撕裂和透明性等特性,适用于吹膜、挤出、流延用热封层以及食品包装、卫生医疗、个人护理等领域。
根据溶剂状态的不同,POE聚合工艺可分为溶液法聚合、悬浮聚合以及气相聚合工艺。POE的生产通常采用溶液聚合工艺。
相对于其他类型的聚合工艺,溶液聚合工艺在共聚单体类型、共聚单体相对数量和反应温度方面具有更广泛的操作范围,因而被生产商广泛采用。
溶液聚合工艺除了用来生产乙烯基POE/POP、丙烯基POE、三元乙丙橡胶(EPDM)和烯烃嵌段共聚物(OBC)等特殊聚合物产品外,还可以生产线性低密度聚乙烯(LLDPE)、中密度聚乙烯(MDPE)和高密度聚乙烯(HDPE)等产品。
目前全球POE生产商主要有陶氏、北欧化工、埃克森美孚、三井化学、LG化学等公司,合计产能为238.7万吨/年。全球POE和POP生产商及产能情况详见表。
全球POE和POP生产商及产能情况
公司及装置地址
|
产能,万吨/年
|
商标名称
|
技术路线
|
产品类型
|
陶氏化学
|
美国得克萨斯州
|
45.5
|
Affinity
|
Insite+CGC
|
POE/POP
|
Engage
|
Versify
|
美国路易斯安那
|
23.5
|
Engage
|
Insite+CGC
|
POE/POP/OBC
|
Infuse
|
沙特萨达拉
|
20
|
Engage
|
Insite+CGC
|
POE
|
西班牙
|
6.5
|
Affinity
|
Insite+CGC
|
POE/POP
|
埃克森美孚
|
美国洛杉矶
|
13.5
|
Exact
|
Exxpol
|
POE/POP/EPDM
|
新加坡裕廊岛
|
30
|
Exact
|
Exxpol
|
POE/POP/EPDM
|
LG化学,韩国大山
|
29
|
Lucene
|
专有茂金属催化剂
|
POE
|
北欧化工,荷兰赫仑
|
11.8
|
Queo
|
专有茂金属催化剂
|
POE/POP
|
三井化学
|
日本
|
9.9
|
Tafmer
|
专有茂金属催化剂
|
POE
|
新加坡裕廊岛
|
20
|
Tafmer
|
专有茂金属催化剂
|
POE/POP/EPDM
|
SSNC,韩国蔚山
|
23
|
Various
|
Nexlence
|
POE/LLDPE
|
SCG-DOW,泰国马塔府
|
22
|
Affinity
|
Insite+CGC
|
POE/POP
|
合计
|
256.7
|
|
|
|
陶氏是目前全球最领先的POE/POP生产商,其独资和合资公司的POE/POP总产能为97.5万吨/年,占全球总产能(256.7万吨/年)的38%。
早在20世纪60年代中期,陶氏就开发了DowlexTM溶液工艺,采用两台连续搅拌釜式反应器(CSTR)。
1993年,陶氏对DowlexTM溶液工艺的反应器和换热系统进行改造,采用限定几何构型茂金属催化剂(CGC)和专有的Insite溶液聚合技术,在聚合温度90~200℃、聚合压力1~5MPa条件下,以Isopare(混合烷烃)为溶剂,开发出乙烯/1-辛烯聚烯烃弹性体(POE),牌号为EngageTM;后来又开发出乙烯与丙烯、1-丁烯共聚聚烯烃弹性体,牌号为VersifyTM、AffinityTM。
在全球光伏市场持续增长趋势下,陶氏在2019年推出光伏级ENGAGE™PVPOE系列产品,用其制备的顶部和底部光伏封装胶膜可显著提高光伏发电量、电池可靠性和使用寿命以及抗电势诱导衰减(PID)性能,尤其适用于高效双面光伏电池用胶膜,从而降低度电成本(LCOE)以及光伏电池的总系统成本。
目前,陶氏有两个主要牌号用于光伏组件封装胶,分别为ENGAGE™PV8669(密度为0.873g/cm3,熔融指数为14g/10min)和ENGAGE™PV8660(密度为0.872g/cm3,熔融指数为4.8g/10min),均为乙烯和1-辛烯共聚物。
下表对全球主要POE生产商Dow、ExxonMobil、Mitsui、Borealis、SABICSK的生产工艺参数进行了比较。5家公司工艺各具特色,其中陶氏和埃克森美孚工艺最具代表性,采用双重级联连续搅拌釜式反应器(CSTR),单套产能达到40万吨/年。
公司名称
|
Dow
|
ExxonMobil
|
Mitsui
|
Borealis
|
SSNC
|
工艺
|
DowlexTM
|
溶液
|
溶液
|
BorceedTM
|
NexleneTM
|
单套装置产能,万吨/年
|
≦40
|
≦40
|
≦12.5
|
≦12
|
≦23
|
反应器类型及配置
|
①双重级联CSTR;②双重级联环管
|
双重级联CSTR
|
双重级联CSTR
|
单CSTR
|
双重级联环管
|
反应溶剂
|
Isopare
|
异己烷
|
己烷
|
己烷
|
环己烷
|
反应温度,℃
|
130~150
|
≤200
|
150
|
<200
|
<200
|
反应压力,MPa
|
2~4
|
10~13
|
<4
|
<12
|
-
|
物料停留时间,min
|
①30;②17
|
10
|
30~60
|
10
|
2
|
为解决釜式反应器不易散热的问题,陶氏公司还研发了新的环管溶液聚合反应器,不仅解决了反应器散热的问题,并且提高了聚合物浓度和单体转化率,最终提高了生产效率。
POE通常由茂金属、镍系、钒系等催化剂催化乙烯与高碳α-烯烃无规共聚获得,目前主流的POE催化剂有三类:限定几何构型茂金属催化剂(CGC)、桥连双配体结构茂金属催化剂以及非茂金属催化剂—苯氧基亚胺催化剂(FI)。
1993年陶氏公司采用高温溶液法Insite工艺,通过CGC催化剂首次生产出窄分子量分布(MWD)、长链支化的高性能POE。依据催化剂桥基的不同,CGC催化剂分为硅桥CGC、碳桥CGC、杂环CGC等类型。
总体来看,目前对茂金属催化剂的研究已相当全面,能够通过控制催化剂的结构和对称性来控制产品的结构与性能。非茂金属催化剂由于其配体和金属活性中心的选择范围更为广泛,为催化剂的设计和合成提供了更大空间,能够合成不同拓扑结构的聚烯烃新产品,因此非茂金属催化剂是未来POE催化剂领域又一重要研究方向。
全球POE消费现状分析
根据IHSMarkit数据,2021年全球POE和POP的总消费量约170万吨,其中POE消费量89万吨,POP消费量81万吨。基于乙烯基POE/POP的消费量约为140万吨;基于丙烯基POE/POP的消费量仅为30万吨。
2021年,全球POE主要消费在热塑性聚烯烃(TPO)材料领域,其中车用和非车用TPO消费量分别占40%、27%,电线和电缆领域占13%,泡沫材料领域占比5%,其他领域占13%,包括挤压和模制产品、光伏胶膜、医疗、薄膜、粘合剂、噪声振动抑制应用和鞋类等。
POE是汽车部件应用的首选材料,可作为三元乙丙橡胶(EPDM)弹性体组件的替代品。目前,POE已经替代大部分的EPDM用于生产汽车内饰件和外饰件,其占POE总需求的40%,内饰件包括控制台盖、膝垫、仪表板蒙皮、门板、支柱成型件和座椅,外饰件包括前端车身面板、门槛板、侧饰条和保险杠饰板。
加入乙烯基POE树脂,可使汽车部件具备出色的抗低温冲击性能。
丙烯基POE与聚丙烯的相容性高,也能提高材料的抗冲击改性性能。
从全球POE的消费趋势来看,随着POE产品性能的持续改进和应用领域的拓展,预计未来5年POE的年均需求增速为5%~6%,其中中国、印度、南美和东南亚地区的需求增长较快。
随着全球光伏装机的持续快速增长和POE胶膜渗透率的提升,光伏胶膜已经成为POE消费需求增长最快的领域。
共挤型POE胶膜(EPE胶膜)是将EVA材料和POE材料进行复合改性,由EVA-POE-EVA胶膜通过共挤工艺制造而成,既保留了EVA材料的层压工艺便利性和高粘结性,也兼具POE材料的高阻隔和耐候性能,适用于HJT电池(异质结电池)组件的粘结。
EPE胶膜抗PID性能好,对于单晶PERC电池背面及N型单晶电池正面抗PID性能优异,具有较高的阻水能力、耐UV、耐湿热老化等综合性能,并且产品性价比高,优于常规纯POE胶膜,可节省POE用量,解决胶膜原材料供应瓶颈问题,其在未来光伏胶膜的消费中也将占据重要地。
目前我国POE技术研发与投资活动十分活跃,其中一些项目处于中试阶段,也有一些项目进入工业装置建设阶段,另外还有一部分项目处于规划阶段,总生产能力约240万吨/年。
序号
|
企业名称
|
产能,万吨/年
|
项目进展
|
投产时间
|
1
|
万华化学
|
2*20
|
完成中试,工业装置在建
|
2024
|
2
|
卫星石化
|
10
|
完成中试,工业装置在建
|
2024
|
3
|
天津石化
|
10
|
完成中试,工业装置在建
|
2024
|
4
|
京博石化
|
5
|
完成中试,工业装置在建
|
2024
|
5
|
茂名石化
|
5
|
完成中试,工业装置在建
|
2025
|
6
|
东方盛虹
|
30
|
中试阶段
|
2025
|
7
|
中国石油
|
10
|
中试阶段
|
2026
|
8
|
青岛诚志股份
|
2*10
|
项目报批阶段
|
2025
|
9
|
辽宁鼎际得石化
|
40
|
筹建阶段
|
2027
|
10
|
惠生工程
|
10
|
规划阶段
|
-
|
11
|
荣盛石化
|
2*20
|
规划阶段
|
-
|
12
|
湛江中捷精创
|
10
|
规划阶段
|
-
|
13
|
中能高端新材
|
10
|
规划阶段
|
-
|
合计
|
|
240
|
|
|
目前已经完成POE中试的公司有万华化学、卫星石化、天津石化、京博石化、茂名石化等,其工业装置处于建设阶段,总产能70万吨/年,预计2024—2025年建成投产;
东方盛虹、中国石油POE项目处于中试阶段,依据中试结果,预计其工业装置(总产能40万吨/年)在2025-2026年建成投产;
处于报批、筹建阶段的项目包括青岛诚志、鼎际得石化,其工业装置(总产能60万吨/年)预计2025—2027年建成投产;
另外还有惠生工程、荣盛石化、湛江中捷精创、中能高端新材等多家公司的项目处于规划阶段,规划总产能约70万吨/年。
总体上目前国内计划建设POE工业生产装置的企业较多,大部分配套1-辛烯原料装置,但部分企业技术不够成熟,仍需进一步进行中试。
从这些项目规划的投产时间分析,我国POE项目将从2024年开始陆续建成投产,进入产能集中释放期,如果这些项目均按期建成,估计到2025年产能将达到约120万吨/年,届时将会有稳定的产品供应投放市场,满足国内消费需求。
目前国内没有厂家宣布计划生产POP,但由于POP与POE是共线生产,所以在POE实现国产化后,原则上也可以生产POP。
近年来,我国汽车轻量化、以塑代钢、光伏、人造草坪等新兴行业的高速增长,带动POE需求的爆发式增长。
特别是在光伏行业高速发展的驱动下,POE消费需求十分强劲,2022年总消费量约68万吨,其中改性塑料领域消费占比52%,光伏领域消费占比为26%,鞋材领域占比18%。
2022年中国POE消费领域分布(数据来源:隆众咨询)
根据中国光伏行业协会数据,目前我国POE光伏胶膜的市场渗透率已达到27%~30%,POE胶膜年需求量在30万吨左右。
由于POE光伏胶膜具有体积电阻率低、水汽透过率低、耐老化性能好、电势诱导衰减小等优点,其市场渗透率有望将进一步提高。
根据行业估计,在保守情形下,国内POE胶膜需求将从2021年的26万吨增长至2025年的约57万吨;在乐观情形下,2025年POE胶膜需求量将达到约73万吨,需求量是2021年2.4倍。
由于之前没有POE工业生产装置,国内POE供给全部依赖进口,2022年进口量68万吨,进口价格在22000~28000元/吨,主要来自美国、中东、日本、韩国、新加坡及欧洲等国家和地区,生产商主要为陶氏、埃克森美孚、三井、沙比克、北欧化工等。
国内POE下游消费增长最快的领域是光伏胶膜,随着双玻组件、双面电池的大规模应用,预计POE消费将保持旺盛增长态势,尤其是POE多层共挤胶膜在光伏中的使用会进一步提高。
从我国POE整体消费趋势分析,除了光伏胶膜领域外,汽车用改性塑料领域对POE的消费需求潜力也很大。
目前国外汽车保险杠的共混改性大部分采用POE弹性体,而我国仅有20%左右的保险杠材料采用POE。我国汽车和塑料行业的生产体量巨大,新能源汽车材料轻量化发展不断提速,预计未来POE在车用材料领域的消费需求将进一步扩大。
(1)从市场需求角度看,光伏胶膜消费总体呈现旺盛增长趋势,POE胶膜和EPE胶膜的消费占比将不断增加
我国EVA光伏胶膜产业经过多年的发展,正在加速替代进口产品,成为全球光伏胶膜市场的主导力量,市场集中度较高,福斯特、海优新材、斯威克等企业占据国内主要市场份额。
根据中国光伏个行业协会数据,目前EVA胶膜仍为主流封装材料,约占64%的市场份额,但POE胶膜和共挤型EPE胶膜因其高抗PID性能和高阻水性能,能够适用于双玻组件和新一代太阳能电池技术,市场需求逐年增长,2022年POE胶膜和EPE胶膜合计市场占比提升至35%,未来二者市场占比将进一步增大,到2030年将超过EVA胶膜的市场份额,达到约50%。
光伏胶膜产业的发展方向主要受下游光伏装机需求、新一代太阳能电池技术发展和双面组件市场份额提升等因素的影响。
根据国家能源局公开的数据,2022年光伏发电装机突破3.93亿千瓦,风电3.65亿千瓦,距离到2030年风电和太阳能发电总装机容量达到12亿千瓦以上的目标仍有一定距离。
另外,根据2021年10月国务院印发《2030年前碳达峰行动方案》,到2025年,新建公共机构建筑、新建厂房屋顶光伏覆盖率力争达到50%,由此来看预计光伏产能仍将继续保持快速增长,进而带动光伏胶膜等相关原材料需求量不断扩大。
随着国家对光伏行业的政策支持和市场潜力的释放,预计到2030年,我国新增光伏装机将在120~140吉瓦,光伏胶膜市场规模将达到172~201亿元。
(2)从产品替代角度看,POE和EVA胶膜均有各自的优势和需求,未来将呈现EVA、POE、EPE三种胶膜共存的局面
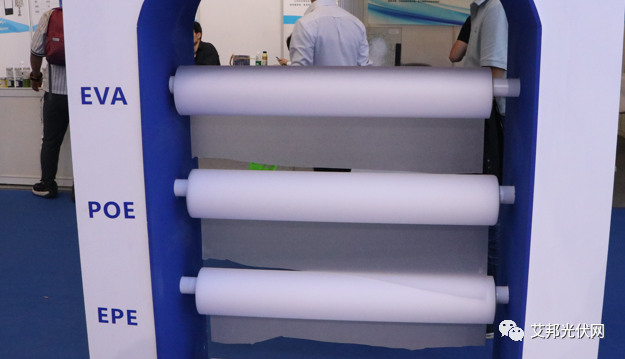
近年来,成本相近而发电效率更高的太阳能双玻组件逐渐被市场所接受,但由于电池减薄、双玻组件压缩框架材料导致水汽进入,潜在致降解(PID)衰减问题比较严重。
POE胶膜具有优异的水汽阻隔性,可以大幅度提高抗PID性能,规避EVA胶膜的弱点,目前业界普遍使用POE单独或者POE与EVA复合来解决PID问题。
POE材料也有其自身的缺点,主要是使用过程中容易产生气泡、光伏组件层压良率低,而且材料严重依赖进口,采购成本较高,产品和原料供应不稳定。
综合来看,POE胶膜和EVA胶膜在不同的细分市场上均有各自的优势和需求,POE胶膜只是部分替代EVA,不太可能完全替代EVA胶膜。
预计短期内,光伏封装胶膜将仍然主要使用透明EVA及白色EVA。白色EVA胶膜相比透明EVA胶膜具有更高的反射率,主要应用在单面发电光伏组件的背面,对于单玻和双玻组件可分别实现1~3W和7~10W的功率增益。
POE胶膜相比EVA胶膜有更高的水汽阻隔率,可以避免PID现象,有效提升双面组件的抗老化性能。由于EPE共挤膜结合了EVA良好的粘合性能和POE的抗PID性能,被认为是光伏胶膜组件的未来主流趋势。
短期内由于POE市场供应紧张且价格高于EVA产品,POE在光伏封装应用中大量替代EVA占据较大市场份额的可能性很小,但随着2025年国内POE产能释放,POE的性价比将逐渐被下游消费者认可,其消费量将得到快速增长。
总体来看,光伏市场将呈现EVA、POE、EPE三种胶膜共存的局面,产品质量和性能也将不断提升,满足不同客户的需求。
(3)从生产技术角度看,聚合单体高碳“-烯烃技术、茂金属催化剂技术、高温溶液聚合技术壁垒逐渐取得突破,加速POE材料实现国产化
POE诞生近30年时间,国内至今未实现工业化生产,主要缘于存在三个核心技术壁垒:
-
一是高碳α-烯烃的自给能力不足;
-
二是茂金属催化剂体系的研究滞后于国际先进水平;
-
在高碳α-烯烃的供应方面,目前国内POE共聚单体1-辛烯生产能力相对较低,掌握其生产技术的企业较少。目前中国石油、中国石化、浙江石化、京博石化、卫星化学等已建成运行1-辛烯合成工业试验装置。总体而言国内1-辛烯生产技术已完全成熟,为POE工业生产创造了良好条件。
中国石油、中国石化、万华化学等均在茂金属催化剂合成POE领域进行了研发布局,申请了多项技术专利,茂金属催化剂合成技术已经趋于成熟,下一步需要加快产业化应用步伐。
在POE高温溶液聚合工艺研究方面,万华化学、京博石化、斯尔邦、卫星化学、中国石化、中国石油等均开展了聚合工艺技术攻关,已进入中试阶段或已完成中试,为工业生产提供成熟条件。
值得一提的是,中国石油石油化工研究院经过多年研发攻关,成功开发出系列α-烯烃(1-丁烯、1-己烯、1-辛烯)成套生产工艺技术,并实现工业应用,同时攻克了POE高温高活性共聚茂金属催化剂制备、高黏体系传质和聚合产物深度脱挥等技术难题,研发出专用POE催化剂和丁烯基及辛烯基系列产品,于2023年5月建成千吨级POE装置并实现中交,下一步将加紧开展中试,为中国石油POE工业装置建设提供技术支持。
光伏封装胶膜作为光伏组件主要材料之一,其消费需求旺盛、市场潜力巨大。整体而言,光伏胶膜的未来发展趋势可归纳为三点:
目前EVA胶膜是光伏封装胶膜市场的主流材料,基于N型电池是太阳能电池未来主要发展方向,在电池N型化、电池功率大型化、盖板玻璃减薄以及双玻组件增多的趋势下,电池封装胶膜技术迭代加快,POE胶膜和多层共挤胶膜(EPE)以其优异的性能,消费需求不断扩大,并加快对EVA胶膜的替代,未来将呈现EVA、POE、EPE等多品种胶膜相互并存的格局。
-
二是POE胶膜进口替代空间大,技术国产化是未来几年关注的热点。
当前EVA胶膜的生产与供给已经完全国产化,并且部分替代进口产品,处于提质扩产阶段,而POE胶膜由于国内技术研发起步较晚,尚不能自主生产,市场消费完全依赖进口产品,在市场需求驱动下,POE技术研发与产业化成为新材料行业关注的重大热点。
-
三是国内POE技术研发及工业化项目投资活跃,即将迎来POE产能释放期。
在我国产业政策指导下,经过能源与新材料行业的努力,POE中试技术攻关进展迅速,聚合单体高碳“-烯烃技术、茂金属催化剂技术以及高温溶液聚合技术壁垒逐渐取得突破,POE工业化装置建设十分密集,2025年将迎来国产POE产能集中释放期,有力支撑POE胶膜技术加快国产化,推动我国光伏产业和新能源行业高质量发展。
参考资料:光伏封装胶膜材料发展现状与前景分析,黄格省等,中国石油天然气股份有限公司石油化工研究院
艾邦将于10月20日在无锡举办“2023年第二届光伏材料论坛”,届时万华化学新材料事业部POE行业经理 韩笑奇将给大家带来“万华创新材料助力光伏行业可持续发展”主题演讲,介绍万华化学POE的量产情况及在光伏胶膜领域的应用情况,敬请期待!
原文始发于微信公众号(艾邦光伏网):光伏封装胶膜POE材料发展现状与前景分析