从电池技术进步的角度来看,金属化作为钝化镀膜的后续工艺,其技术路线选择需要与钝化膜相配套,一方面,金属化本身与钝化膜/硅基体的接触将在很大程度上影响复合;另一方面,栅线本身对电池的光学损失、电阻损失起到至关重要的作用。
对于光伏电池金属化来说,栅线宽度仅是表观指标,不同的浆料设计出发点在于界面接触,其次是印刷性能,以及烧结/固化后的附着特性和焊接特性,最后是工艺与材料的综合成本。
全铝背场电池
全铝背场电池(Al-BSF)是最早实现产业化的晶硅电池结构,具有工艺流程简单、 技术成熟、成本低廉等诸多优点。
但是,电池背面硅/铝的全面积接触引起的载流子复合较为严重,且铝背场层的反射率低,导致长波段光响应差,这些使得 Al-BSF 电池始终无法突破 20%的效率瓶颈。
单面 PERC
随着背表面氧化铝(AlOx)钝化技术的出现,PERC 电池开始全面取代全铝背场 电池。
在单面 PERC 电池中,仍然采用铝背场,同时铝背场通过激光开槽的方式与硅基 体实现线接触,并在接触区域形成局部铝背场(LBSF)。
双面 PERC
在双面 PERC 电池中,放弃了全铝背场,而采用铝线接触的方式。根据 ITRPV 数据,双面 PERC 电池铝浆耗量仅为单面 PERC 的 1/4。
TOPCon 与 HJT 电池
由于采用了钝化接触技术,金属电极不再与硅基体直接接触,大幅改善钝化效果 与金属复合。TOPCon 电池正面采用银铝浆。
原因在于对于 TOPCon 电池,正面仍采用同质 扩散结,且硼掺杂的浓度较磷掺杂低 1-2 个数量级,导致发射区的接触电阻较大。
在 P 型发射极局域重掺硼技术完善之前,TOPCon 电池正面采用了银铝浆,在 烧结中铝原子进入 P 型发射区形成 p+区域,起到选择性发射区(SE)的作用。
对于金属化工艺来说,重要的是工艺与材料的匹配。丝网印刷、钢板印刷、激光 转印三种工艺都适用于液体浆料,适配高温银浆、低温银浆、银包铜银浆。
而无 主栅技术、铜电镀则跳出了液体浆料的范畴,单独具备一套工艺与材料。
1.金属化之材料:浆料区别与改进路线
根据 ITRPV 《2022 年国际光伏技术路线图》,2021 年,200GW PERC 电池(效 率 23%)消耗银 2640 吨,约占全球银总供给的 8%,单耗约 13.2mg/W。
2.高温浆料:从 PERC 浆料到 TOPCon 银浆
从 PERC 电池到 TOPCon 电池,从结构上看仅仅是背表面钝化方式发生了改变, 但由于硅基底从 P 型转变为 N 型,以及钝化层的改变,造成金属化工艺的较大 转变。
正面:对于典型的 N 型 TOPCon 电池来说,主要是从 N 型发射极(磷扩)转变 为 P 型发射极(硼扩),钝化方面仍采用 SiNx 和 AlOx 层。
但由于硼扩掺杂浓 度低,为了实现更好的接触,正面细栅从银浆转变为银铝浆。
背面:由于钝化接触结构解决了金属与硅基体接触的问题,TOPCon 电池的背面 不再需要激光开槽+铝浆(LBSF),而是采用了银浆细栅。
整体来看,TOPCon 银浆主要分三种细分应用:
1)正面细栅浆料(银铝浆,烧穿型),需要在烧结过程中烧穿 SiNx 和 AlOx 层, 与硼发射极接触;
2)背面细栅浆料(银浆,烧穿型),需要在烧结过程中烧穿 SiNx 层,与 poly 硅层接触;
3)正背面主栅浆料(银浆,非烧穿型),主要起连接细栅、汇聚电流、辅助焊 接作用。
但是,TOPCon 银浆正背面细栅需严格控制烧穿深度。
对于正面细栅,需控制银铝尖刺的深度,否则容易破坏硼发射极;对于背面细栅,需控制烧穿深度,特别是在 poly 层减薄的趋势下,如何与薄 poly 层形成配合至关重要。
在高温银浆中,玻璃粉起到刻蚀作用,因此工艺核心之一在于调节玻璃粉的成分 与配比。玻璃粉在烧结过程中主要有两个作用:
1)刻蚀硅片表面的 SiNx 减反射涂层,在烧结过程中促进硅太阳能电池正面电极的致密度,从而形成致密的导电网络,使得银膜与硅基片形成良好的欧姆接触;
2)银浆烧结过程,玻璃粉在高温下溶解银粉,并带着银粉重新排列,这将影响银浆的整个烧结过程。
3.低温浆料与银包铜
由于异质结电池中非晶硅不耐高温,导致其需适用低温银浆。与高温正银相比, 低温银浆固化温度低,不含玻璃粉,属于非烧穿型浆料。
在高温银浆中,玻璃粉会首先发生熔融,刻蚀硅片表面的 SiNx 减反射涂层并带 动银粉重新排列。
因此玻璃粉是技术核心,助力实现高效接触和高效银粉导电。
在低温银浆中,由于取消了玻璃粉,银粉粘结主要靠有机体系树脂固化收缩实现。
由于缺乏烧结步骤,有机组分(特别是树脂)残留在浆料中,这也是低温银浆电 阻率较大的根本原因。
采用片状银粉+球状银粉复配的方式,有助于提高银粉间接触面积,从而改善银 浆导电性能。但同时影响了印刷速度。
印刷速度是规模制造、产能提升的关键。
HJT 低温银浆印刷与铺墨速度(CT>2s) 显著低于主流的单晶 PERC、TOPCon 高温银浆。
银包铜
由于低温银浆导电性较差,加上双面使用银浆,使得 HJT 电池的单位银浆耗量 约为 PERC 电池的 2 倍,拉大了成本方面的差距。
银包铜作为一种有效的降本手段,引起业界重视。
银包铜粉是一种核壳结构材料, 具有铜的物化性能和银的优良金属特性以及高导电性、抗氧化性和热稳定性,既节约贵金属又降低了成本。
由于高温下铜容易氧化,因此银包铜浆料目前仅适用于异质结电池。
制备技术路线方面,化学镀法具备工艺简单、成本低等优点,目前已成为主流路 线。工艺方面根据沉积机理不同,又分为还原法和置换法两种。
运用化学镀法制备银包铜粉的过程中,镀液的主要成分是由硝酸银溶液组成,并与铜离子发生置换反应,游离的银离子因为有较高的氧化-还原电位,导致镀液稳定性不佳,制得的镀层不够致密。
因此,现代工艺多采用络合剂来络合游离的 银离子,提高银离子的络合常数,保证镀液在金属包覆过程中的稳定性。
常见的络合体系包括:氨水络合体系、EDTA 盐体系、胺烯类化合物体系。
4.银浆与银粉国产化
不管是高温银浆,还是低温银浆,都是以银粉作为导电相。
银粉在太阳能电池导 电银浆中占质量的 70%~90%,是决定银浆和形成银电极性能的关键因素。
银粉作为一种功能性粉末,不仅继承了银单质的一些性质,同时还具有粉末的独 特性能,所以银粉的形貌、粒度分布、分散性、表面性质等都对银浆的性能具有 重要影响。
1)粒度分布。
在 0.5~5.0µm 之间的银粉比较适用于太阳电池用银浆的调制。
且在银浆调制过 程中,合理搭配不同粒度分布的银粉,可降低银浆印刷塑性后银粉自然堆积状态 下的空隙率,进而减小银浆烧结后导电膜的孔隙率及形成的电路中的串联电阻。
2)分散性。
银粉的分散性直接影响银浆的调制效果,分散性好的银粉在银浆调制过程中能与 有机体系充分润湿、混合,均质分散在有机载体中,使银浆具有很好的触变性和 流平性,丝网印刷过程中能连续、流畅、均匀地通过网孔,形成完整的电路图案, 有利于实现大规模连续生产。
3)振实密度。
银粉的振实密度直接反映了银粉在生成过程中结晶的完整度。
振实密度越高的银 粉,其结晶完整度越好,在自然状态下银粉颗粒之间的堆积越致密,空隙率越小, 调浆烧结后得到的导电膜的空洞少且小,电路中的串联电阻小,电极导电能力优 良。
在 PERC 时代,正银主要采用球形银粉,背银采用片状银粉。
其中背面银浆的技 术要求较低,从原料端的片状银粉到产品端的背面银浆基本都已实现国产化。
尽 管 P 型电池正面银浆的国产化率在 2021 年末已达到 61%,但正面银浆所用的 银粉大多仍依赖进口。
n 型电池用正银国产化程度明显提升。受制于市场规模以及技术等因素影响,当 前 n 型电池的正面银浆国产化程度开始出现较大的分化。
2021 年 TOPCon 电池 用正面银浆国产率达 70%左右;HJT 电池用低温主栅银浆国产率 10%左右,细 栅用银浆依然全部依赖进口。
国外银粉制造厂家主要集中于日本和美国,销量较大的有日本 DOWA、日本德力化学、美国 Ferro 和 Ames Goldsmith 等公司。
银粉国产化率远低于银浆国产化率。原因在于银浆工艺核心在于配比,而银粉的 制造则具备更高的壁垒,特别是低温银粉对比表面积、分散性、平均粒径、振实 密度等参数要求更高。
金属化之工艺:接触式与非接触式
1.接触式
根据中国光伏产业协会数据,目前电池片的金属栅线几乎全部通过丝网印刷的方 式制备,2021 年市场占比达到 99.9%。
预计未来 10 年内丝网印刷技术仍将是主流技术。丝网印刷由五大要素构成:工作台、丝网、刮刀、浆料、基片。
基片直接放在带 有模板的丝网下面,丝网印刷油墨或涂料在刮刀的挤压下,从图形部分的网孔中 间挤压到基片上。
印刷过程中刮板始终与丝网模板和基片呈线接触,接触线随刮 刀移动而移动,其他部分与基片为脱离状态,保证印刷尺寸精度和避免蹭脏基片。
分步印刷(DUP)&两次印刷(DP)
两次印刷:先印刷第一层银浆并烘干,在第一层银浆的基础上覆盖第二层银浆,两层共烧结 形成电极。
两次印刷的方法可以突破单次丝网印刷高宽比的天花板,能有效提高电极栅线的 高宽比,既能增加电池的受光面,又能降低栅线电极整体的线电阻,从而大幅提 升电池的光电转换效率。
分步印刷:根据主栅与细栅线对浆料特性要求的不同,将主栅与细栅分开印刷。细栅采用主 流的正面电极银浆,具有较好的塑形能力和良好的烧结特性及欧姆接触。
由于主 栅在电池片上主要作用是汇集细栅上的电流,对塑形能力的要求较低,因此可选 用较便宜的银浆。
同时分开印刷后主栅网版可以采用与细栅规格不同的网版,可 进一步降低主栅线的银浆单耗。
多主栅:从 MBB 到 SMBB
主栅是指晶硅太阳能电池表面上的粗电极条,起到连接细栅,将电池体内产生的 光生电流引到电池外部的作用。
多主栅技术(MULTI-BUSBAR,MBB)是通过 提高主栅数目,提高电池应力分布均匀性,进而提高导电性,增加转换效率。
综合来看,多主栅技术(MBB)具有电学和光学两方面优势。
电学优势:
1)MBB 电池片电流横向收集路径增加,较传统 5BB 提高 30%以上;
2)MBB 技术可以使电流流经细栅到达主栅的路径显著缩短 50%以上,有效减 少电流流经细栅产出的功率损耗;
3)MBB 技术提高了电流的收集能力,即多主栅对电池片隐裂、断栅、破裂等容 忍度更高。
光学优势:多主栅组件设计中,由于单根焊带变细,一般选用圆形焊带进行电池片连接,相 对与扁平型常规焊带,圆形焊带更能体现光学上的优势。
圆形焊带的使用,使得入射光无论从哪个角度进入,都能在焊带区域获得约 75% 的利用率,而传统的 5BB 采用的平焊带对入射光的综合利用率仅 5%以内。
理论上来说,SMBB 是 MBB 技术的升级版,延续了 MBB 的诸多优点,通过采 用更细的栅线,实现更少的遮挡和更短的电流传输距离。
从而有效降低了串联电 阻,并进一步提高了对电池对隐裂、断栅、破裂的容忍度,提高可靠性。
不管是 MBB 还是 SMBB,对于丝网印刷的原理性要求变化不大,与现有设备兼 容。
重要的是主栅增多,焊丝变细,焊点变小,对于串焊机的对位精度和焊接精 度要求提升。
同时,由于主栅变细,需开发相应的 MBB/SMBB 焊带。
部分厂家相关进展:迈为股份:积极探索新的组件工艺,成功开发出 SMBB 串焊机,可以满足 163、 166、182 和 210 多种规格电池的 SMBB 产品需求,焊丝直径最小可以兼容到 0.25mm;
宇邦新材:公司研发了适用于多栅组件的 MBB 焊带、适用于 HJT 组件的低温焊 带、适用于叠瓦组件的超薄冲孔焊带、适用于微间距组件的异形焊带等。
目前市 场上主流的产品还是 MBB 焊带,SMBB 焊带的市场正在逐步推开。
同享科技:公司除了积极开发常规互连焊带、常规汇流焊带外,也积极探索与研发 SMBB 焊带、黑色汇流带及反光焊带。
公司年产涂锡铜带(丝)15000 吨项目建成后,将形成 8000 吨 SMBB 焊带、4000 吨异形焊带、2200 吨反光汇流焊 带及 800 吨黑色汇流焊带的生产能力。
钢板印刷
传统网版的细栅附着在丝网上,丝网的网节或钢丝会阻挡网版透浆料,导致印刷 后栅线高低起伏、拓宽,影响电性能。
而全开口钢板的细栅部分是 100%的无遮挡结构,网版透浆料更顺畅、栅线更平整、均匀,从而电池栅线的形貌得以优化、 电性能得以提升。
由于栅线印刷区域为全开口结构,印刷高度均匀,在制造相同效率电池的情况下, 净节省 20%左右的银浆。
2.非接触式
激光转印
激光图形转印技术(简称:PTP)是一种新型的非接 触式的印刷技术,该技术在特定柔性透光材料上涂覆所需浆料,采用高功率激光 束高速图形化扫描,将浆料从柔性透光材料上转移至电池表面,形成栅线。
激光转印能够突破传统丝网印刷的线宽极限,轻松实现 25um 以下的线宽,且 印刷高度一致性、均匀性优良,误差在 2um。
作为非接触式印刷,可以避免挤 压式印刷存在的隐裂、破片、污染、划伤等问题。
激光转印包括两个步骤:填充过程和转移过程。填充过程:使用的是带有压花沟槽的透明聚合物薄膜,通过两个具有不同倾斜度 的金属吸水扒胶条将浆料填充到沟槽中。
转移过程:将充满沟槽的薄膜旋转 180°并移至打印位置,电池片放置在薄膜下 方 200μm 处,依次使用波长为 1070nm 的激光照射。
激光辐照通过透明膜,其能量首先被糊剂表面吸收。产生的热能使浆料和沟槽之 间的界面区域中的有机成分汽化,并在浆料/薄膜界面处形成高压蒸汽层。
当在 浆料/薄膜界面处建立足够的压力时,浆料会释放到基材表面上。
无主栅(SWCT)技术
无主栅技术(简称 SWCT)由加拿大 Day4 能源公司由梅耶博格开发和工业化,并于 2013 年正式发布。
其关键技术 在于使用铜线(由锡合金包覆)代替传统主栅,并将铜线嵌于聚合物薄膜之上, 同时实现了细栅电流汇集传输和电池片连接,从而完成对主栅和焊带的替代。
SWCT 技术的优势:
1、提效,原理同 SMBB 技术。
首先,SWCT 技术中用细线代替主栅,相比 SMBB 技术,主栅数量进一步增多,通过缩短细栅电流传输距离,增加电流收集能力从 而实现提效。
其次,SWCT 技术采用圆丝铜线,较传统主栅增加了入射光利用率。
2、降本,实现主栅去银化。
SWCT 技术中采用圆铜线(锡合金包覆),实现了 主栅去银化。
第一代 SWCT 技术使用铟锡合金,第二代技术使用铋锡合金,成 本进一步降低。
同时由于主栅(圆铜线)数量增多,细栅宽度有望实现进一步下 降。
根据 CSEM 数据,相比传统丝网印刷技术,SWCT 技术可以将银耗量降低 85%。
3、免焊接,在层压过程中实现接触。
SWCT 技术中不但省去了主栅印刷,还省 去了焊带焊接过程,在层压过程中实现圆铜线与细栅的接触。
铟锡合金的熔点为 120℃,铋锡合金的熔点为 138℃,因此层压温度低于 140℃即可实现熔融接触。
4、可靠性。
一方面,同 MBB 技术类似,更细密的网格提高了电流的收集能力, 即对电池片隐裂、断栅、破裂等容忍度更高。
另一方面,SWCT 技术对电池片施 加的应力更小,这归功于低温工艺和灵活细线,可有效减少电池片边缘翘曲。
铜电镀
铜电镀实现量产后,有望彻底替代银浆的使用,从而实现有效降本。铜电镀工艺 整体分为图形化和金属化两大环节。
图形化环节:种子层的核心作用是改善 TCO 的附着力,通常采用镍或镍-铜合金。
但镀制的种 子层需要在完成电镀后,进行种子层的回蚀,增加了供需,影响了工艺的量产性。
目前可选择的方法有选择性种子层沉积或无种子层工艺。2022 年 9 月,迈为 &SunDrive 双面微晶无种子层直接电镀效率 26.41%。
图形化的核心环节在于制备选择性沟槽,以便进行下一步电镀环节,目前常见的方法有曝光显影和激光开槽两种。
金属化环节:核心为电镀环节。根据罗博特科公告,目前市面上比较主流的主要是垂直升降式 电镀、垂直连续电镀、水平电镀三个方向。
垂直电镀在 PCB 领域应用广泛,但 缺点在于自动化水平较低;水平电镀自动化程度高,可长时间稳定工作,但技术 要求高,长期为国外垄断。
东威科技光伏电镀路线为垂直电镀,同时掌握水平电镀技术(主要用于 PCB 领 域),公司水平电镀技术为国内首创;
罗博特科的方案区别于垂直升降式电镀、垂直连续电镀、水平电镀三种方案;捷得宝光伏电镀路线为水平链式。
根据公告 和官网信息,东威科技和捷得宝设备产能均达到 6000 片/小时。
铜电镀有望成为光伏电池金属化终极方案。原因在于该技术路线不但可以有效实现降本,而且对光伏电池效率提升亦有帮助。
从栅线形貌来看,铜电镀可以将栅线宽度降至 15μm,高 26μm,外观更加平直。
从接触部位微观结构来看,铜电镀的接触部位较银浆印刷烧结工艺更致密,空隙更少。
END
艾邦建有“光伏产业交流群”,群友有光伏电站、BIPV、光伏组件,电池片、背板,封装胶膜,接线盒、接插件、光伏边框、光伏支架、逆变器、光伏玻璃等零部件以及EVA、POE、PVDF、PPO、PA、硅PC、PET膜、氟材料、光伏银浆、焊带、粘接剂等材料以及相关生产、检测设备的上下游企业。欢迎扫码加入探讨。
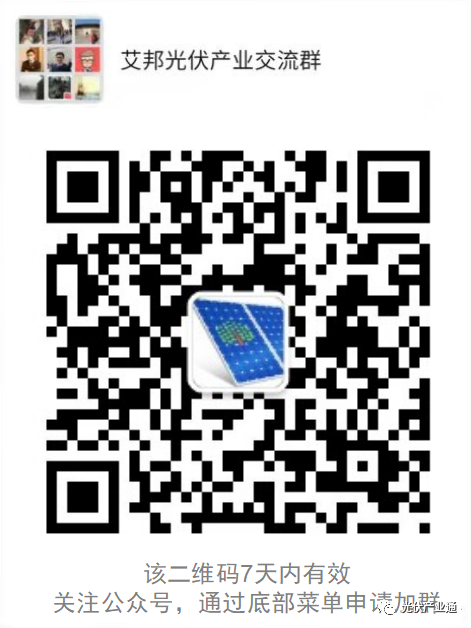
原文始发于微信公众号(艾邦光伏网):光伏电池技术演进与降本关系紧密,金属化工艺“首当其冲”
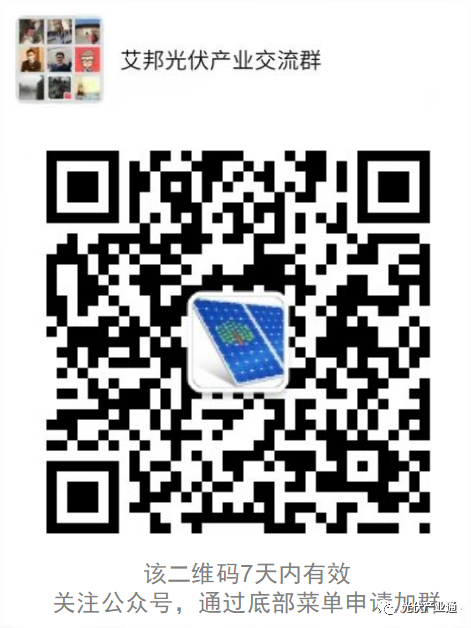