光伏级单晶硅与半导体级单晶硅的纯度相差好几个数量级,光伏级单晶硅的纯度是99.9999%,而半导体级单晶硅的纯度普遍要求10-11个9,即99.99999999%。
目前我国生产的单晶硅料和硅片绝大部分都是光伏级,从产业规模看,光伏产业的全球市场份额在1000亿美元左右的规模,近年的生产和市场增量基本都在我国,但用来做芯片的半导体级芯片,大陆企业的产能占比就骤降到不足5%。
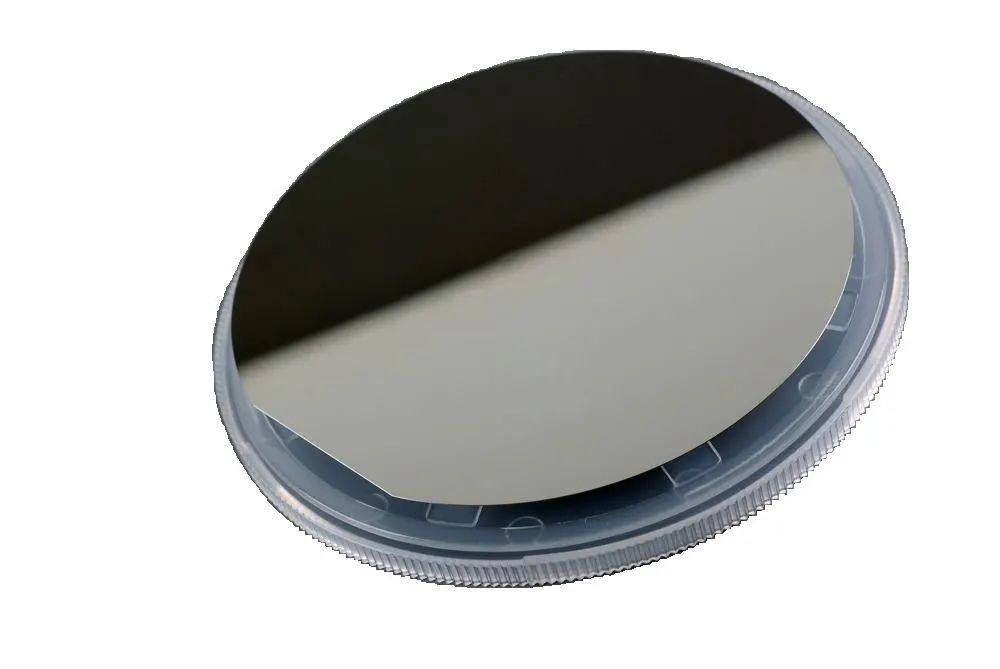
虽然半导体硅片的市场规模只有100多亿美元,但越往下游利润就会以指数级形式增长,芯片的市场规模就高达4000亿美元,整个半导体产业环环相扣。那么硅片是怎么来的?
硅棒截去硅头硅尾,切下来的部分如果质量好还可以切成籽晶,用来拉出新的硅棒,实现硅片生产的无限套娃。接下来用四探针法测量棒身的电阻率,用来检查轴向的杂志浓度是否异常,检测完成后,将其截成30厘米左右长度的硅段。
截成硅段后,进入下到程序滚磨。顾名思义,就是将硅段固定在机器上,让其缓慢滚动,用侧面的金刚石砂轮,简称金轮,对棒身进行打磨,由于直拉法无法精确的控制晶体生长,获得一个完美的圆柱体,所以得拉出一个粗一点的硅棒,再通过滚磨得到想要得目标尺寸。
硅段与金轮得剧烈摩擦会大量加热,需要持续加水降温,滚磨完成后会在硅段的侧面再摸出一个平面,或者一道沟槽,这就是以后硅片上的定位边(flat)或定位槽(notch)。
光刻机需要通过它们来对硅片进行最开始的定位和校准。在业界,定位边还有一个小作用,就是标明硅片的类型和晶向。
接下来要将硅段切片,以前普遍使用内圆切割机,可以理解成带有环形刀片的狗头铡。
优点是切割稳定,切面较平整,但缺点也很明显,效率低,一次只能切一片,而且由于刃口较厚,切割时所耗的硅料较多,并且不适合处理相对更薄的大尺寸硅片。目前主流的切片方式是使用金刚线的多线切割机,也就是用上面固定有金刚石颗粒的钢丝线同时对硅段进行多段切割。
这种线切法虽然不如传统刀片稳定,后续硅片打磨的时间也更长,但胜在切割效率高,损耗低。
切下来的硅片会先经过一遍机械打磨,让表面更加平整,同时让整体变薄。例如12英寸的硅片通过磨片会将厚度减到775微米左右。
部分硅片还要制造背损伤,即人为的制造一个粗糙的背部,比如在背面喷砂或者沉积一层多晶硅,这样故意在底部制造大量晶体缺陷作为陷阱,将后续工艺中不想要的金属杂质困在底层,从而保护上层的器件。
通过倒角机把硅片边缘的直角边磨成圆弧形,这是因为高纯度硅是一种脆性很高的材料,这样处理可以降低边缘处发生崩裂的风险。
除此以外,有弧度的边角在后续的芯片制造工艺中还有两个作用:
一是在光刻时,光刻胶是通过旋转的方式涂抹在硅片表面上的,如果边缘是直角边,光刻胶容易因为离心力在边缘处累积,造成厚度不均,从而影响光刻。
二是在做外延生长时,沉积物也会优先堆积在直角边影响沉积效果,而圆弧状的角可以消除边缘沉积的现象(Edge Crown)。
磨片和倒角完成后,厂商一般会对硅片打上激光标识码,再进行一遍精磨去除10微米左右的厚度,然后会放入溶剂中进行化学刻蚀。
通常使用氢硝酸和氢氟酸腐蚀掉表面约20-50微米左右的厚度来去除之前打磨的过程中硅片积累的机械损伤以及混入硅片表层的磨料。
经过一系列打磨和刻蚀之后,硅片表面已经十分光滑,但用来制造芯片还不够,因为在后续的工序中需要光刻机将图形投影到硅片上,就类似于用投影仪观看小电影,如果幕布不够平整,有起伏的倾角或者局部的凹凸,投放的影像就会变形失真,影响观看体验。
而在光刻中,硅片就相当于幕布,而光刻的图像尺寸和精度都是纳米级的,所以要求硅片表面是一个完美的平面,一点点起伏参差或者局部凹凸都会影响光刻效果。根据04年的国际半导体技术发展蓝图,12寸硅片的整体平整度要小于51纳米,相当于在电影院挂一块IMAX幕布,起伏比一根头发丝还要细。
为了达到这种极致的平坦,需要对硅片进行化学机械抛光(CMP),这一步结合了物理和化学的理综行抛光手段。
具体做法是将硅片装在旋转的抛光仪器上下降到下方,表面薄层会先被研磨液化学氧化,再被抛光垫物理打磨,这一步硅片会再被打薄5微米左右,直到被抛光成完美的镜面,通常对8英寸芯片进行单面抛光,12英寸硅片进行双面抛光,这样就得到一枚抛光片。
最后还要用去离子水和各种化学溶剂进行清洗,去掉制程中粘附在硅片表面的各种尘埃和杂质,这些颗粒物会影响芯片的制造流程,造成芯片的短路或开路。
除了要控制污染物密度之外,其颗粒物大小往往不能超过特征尺寸的一半,所以在先进制程中,能允许的单个颗粒物直径最多只有几纳米,远远大于细菌的尺寸。
在平整度和清洁度之外,硅片还要保证翘曲度、氧含量、金属残余量等指标,要经过电镜检查、光学散射等各种检测达标后,一张硅片才得以诞生。它将被放在充满氮气的密封盒里送往晶圆厂进行后续处理。
除了种类,硅片的尺寸也有很多种,如前面提及的8英寸与12英寸都是业内的习惯叫法,指的是直径200和300毫米的硅片和晶圆,理论上直径当然越大越好,这样单片晶圆产出的芯片更多,并且硅片边缘处的残损芯片(edge die)占比更少,提高了生产良率,分摊了制造成本。但大硅片在工艺和设备上的门槛也更高,目前8英寸广泛应用于90纳米以上的成熟制程如车载传感器和功率器件,12英寸的大硅片则应用于更先进的制程如电脑CPU显卡、手机存储卡。
当前,全球的硅片供应主要由5家公司垄断,分别是日本的信越化工(Shin-Etsu)和盛高集团(Sumco)、中国台湾的环球晶圆(Global Wafers)、德国Siltronic及韩国SK Siltron。
其中,日本是第一个实现了12寸大硅片量产的国家,此后一直保持在硅片上的先发优势。而环球晶圆2011才成立,依靠从中美洗净中美矽晶继承下来的技术积累以及近几年强势的并购扩张迅速成长为硅片市场第三,并且今年下半年,它还将并购第四的Siltronic,届时市占率将超过30%,与信越化工争夺冠军之位。
目前,大陆的半导体硅片产业中,以中环、立昂微以及上海硅产业为主力,其中天津中环股份立足于光伏单晶硅,近年来积极布局半导体级硅片的研发和生产。
杭州立昂微则是专注于半导体,而且既能做硅料和硅片,也能做分立器件的芯片,是国内少数能贯通产业上下游的半导体企业之一,而上海硅产业集团及其子公司上海新昇是目前国内硅片技术的引领者,除了拥有SOI硅片的自主技术以外,在国内厂商只能生产6英寸及以下的硅片时,他们率先在18年开始规模化生产12寸硅片,结束了国内硅片全靠进口的历史。
不过因为投入成本巨大,而且良率不高,沪硅产业的大硅片到今年还没实现盈利,这也是硅片国产化的第一个难点:成本。半导体硅料和硅片属于上游市场,规模不大,利润不高,但是投入巨大,成本高昂,需要大量资金支持。
第二个难点是设备。以最源头的单晶炉为例,各大硅片寡头都有自己的独家供应商,信越化工甚至能自己制造单晶炉,而后续的生产流程,国内的硅片厂商基本都采用进口设备,比如倒角机主要来自日本的东京精密和大途电子,多线切割机主要来自日本的NTC以及瑞士的SlicingTech,这些设备虽然能够找到国产替代,但质量和精度往往差距较大。尤其是关键步骤的CMP,物料部分如抛光垫和研磨液尚能国产,但设备本身目前完全依赖进口。
第三个难点在于晶圆厂对硅片寡头的路径依赖,从光秃秃的硅片变成包含数百枚芯片的晶圆,这中间要经历动辄数十门设备,上千道工序,成本巨大,所以从源头的工艺验证阶段,晶圆厂就要和硅片供应商紧密合作,而一款工艺成熟以后,晶圆厂就不会贸然更换其他供应商的硅片,否则生产良率和芯片可靠性一旦受影响,成本和代价就太大了。除此之外,研发投入和人才培养也是需要大笔投入。
艾邦建有“光伏产业交流群”,群友有光伏电站、BIPV、光伏组件,电池片、背板,封装胶膜,接线盒、接插件、光伏边框、光伏支架、逆变器、光伏玻璃等零部件以及EVA、POE、PVDF、PPO、PA、硅PC、PET膜、氟材料、光伏银浆、焊带、粘接剂等材料以及相关生产、检测设备的上下游企业。欢迎扫码加入探讨。
推荐阅读:
原文始发于微信公众号(光伏产业通):十个步骤了解硅片制造工艺