电势诱导衰减(PID)最早于2005年由美国Sunpower公司发现并提出。
PID是指光伏组件在电势差的作用下使边框、玻璃与太阳电池之间存在漏电流,导致光伏组件实际输出功率低于其标称功率。
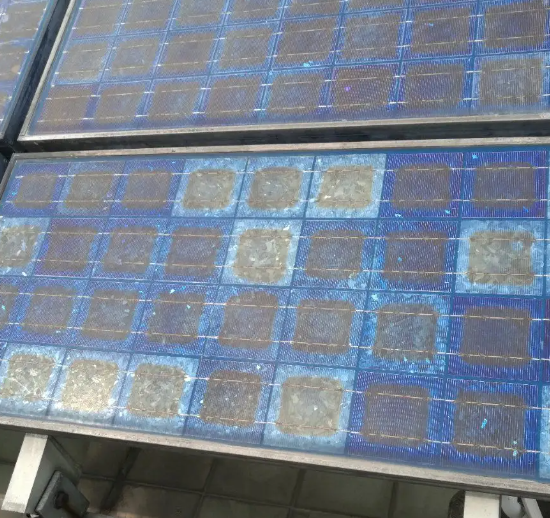
目前,国内外光伏电站针对光伏组件PID现象采用的方案主要有3种,分别是:
-
提高光伏组件内太阳电池串的电压(即将太阳电池串负极接地,光伏组件与其边框之间形成正向偏压);
-
夜间向光伏组件施加反向电压;
-
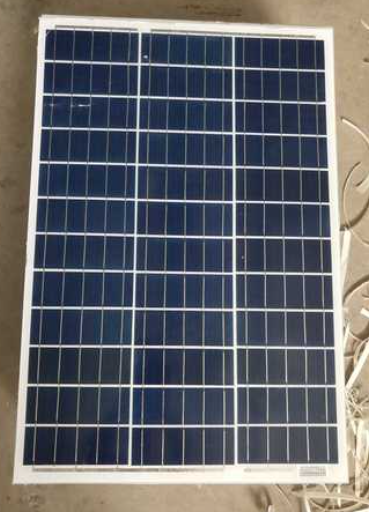
其中,提高光伏组件内太阳电池串电压的方案为事前预防方案,虽然可以起到一定的防PID效果,但对于安装在工商业屋顶的屋顶分布式光伏发电项目来说,存在安全隐患;
夜间向光伏组件施加反向电压为发生PID后进行修复的方案,需增加修复设备,且修复效果存在不确定性,因此,以上3种方案中,优化光伏组件抗PID性能,提高其自身抗PID能力是最直接且经济的方案。
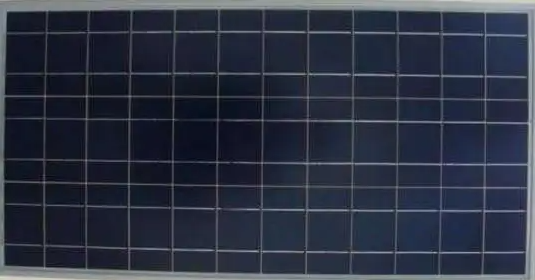
为优化光伏组件抗PID性能,业内研究人员先后尝试了在太阳电池表面改变基极电阻率,改变减反射膜SiN的比例、厚度及致密性,但均无法在太阳电池的光电转换效率与光伏组件的抗PID性能之间取得较好的平衡。
最后有研究发现,在等离子体增强化学气相沉积(PECVD)前,通过热氧化形成一层纳米级厚的SiO2膜,可使光伏组件的抗PID性能有一定提升;
但该工艺较复杂,且抗PID效果存在不稳定性,因此,提升封装胶膜内带电离子阻隔能力成为另一种优化光伏组件抗PID性能的选择。
为对比不同类型封装胶膜的技术性能,选取同一厂家生产的3类不同分子结构的封装胶膜进行对比测试。
每类封装胶膜各取3个批次的样品,分别测试体积电阻率及水蒸气透过率。
不同分子结构封装胶膜的体积电阻率测试结果如表1所示,水蒸气透过率测试结果如表2所示。
表1 不同分子结构封装胶膜的体积电阻率测试结果
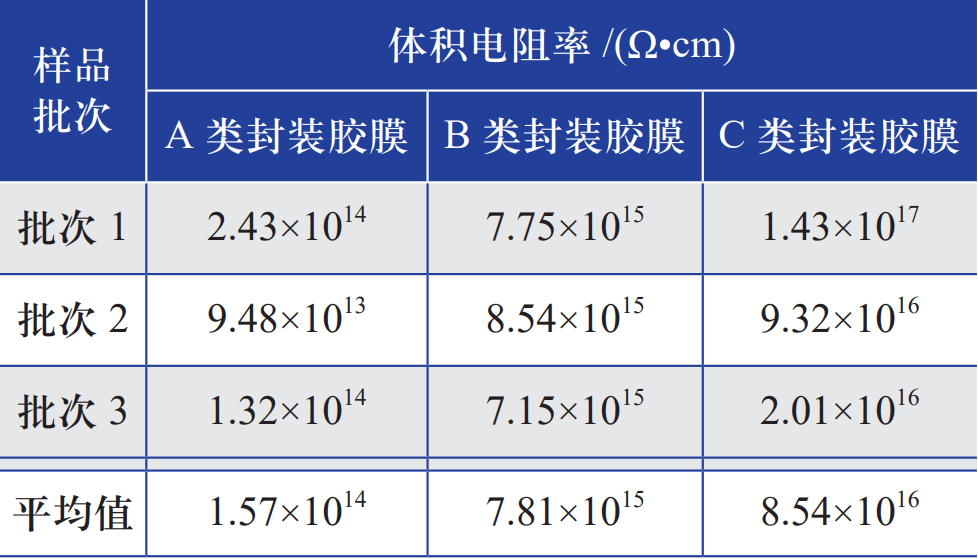
从表1可以看出:不同分子结构封装胶膜的体积电阻率从高到低的排序是C类封装胶膜>B类封装胶膜>A类封装胶膜,即POE>高阻助剂型EVA>普通EVA,且POE的体积电阻率比普通EVA的高约2个数量级,高阻助剂型EVA的体积电阻率比普通EVA的高约1个数量级。
表2 不同分子结构封装胶膜的水蒸气透过率测试结果
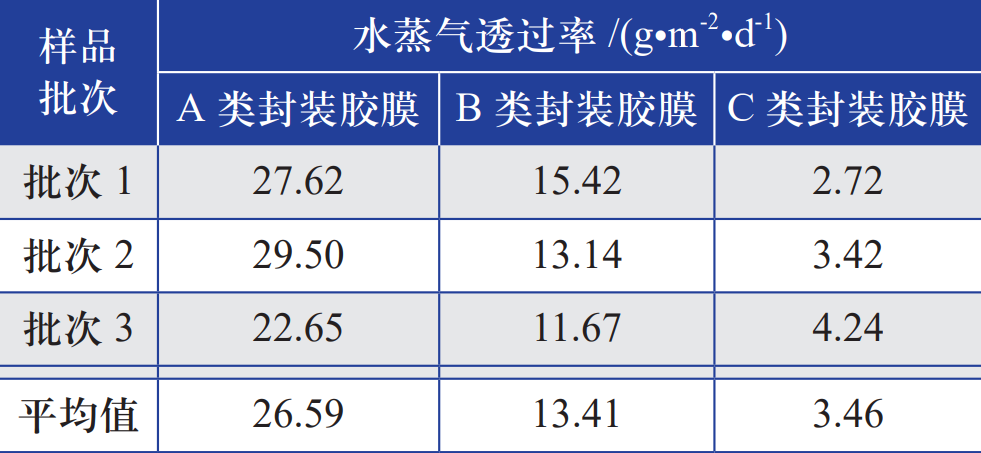
从表2可以看出:不同分子结构封装胶膜的水蒸气透过率从低到高的排序是C类封装胶膜<B类封装胶膜<A类封装胶膜,即POE<高阻助剂型EVA<普通EVA。结合表1的结果,说明不同分子结构的封装胶膜的体积电阻率越高,水蒸气透过率越低。
选取A、B、C这3类封装胶膜3个批次的产品,然后各封装1块光伏组件,共组成9块光伏组件样品。
需保证这些光伏组件样品除封装胶膜外,其他材料及工艺均一致,太阳电池选择膜折射率为2.03的非抗PID型太阳电池,玻璃选择厚度为3.2mm的常规镀膜玻璃,背面采用市场主流的KPF结构背板。
采用不同类型封装胶膜封装的光伏组件最大输出功率Pmax的测试结果如表3所示。
表3 采用不同类型封装胶膜封装的光伏组件最大输出功率的测试结果
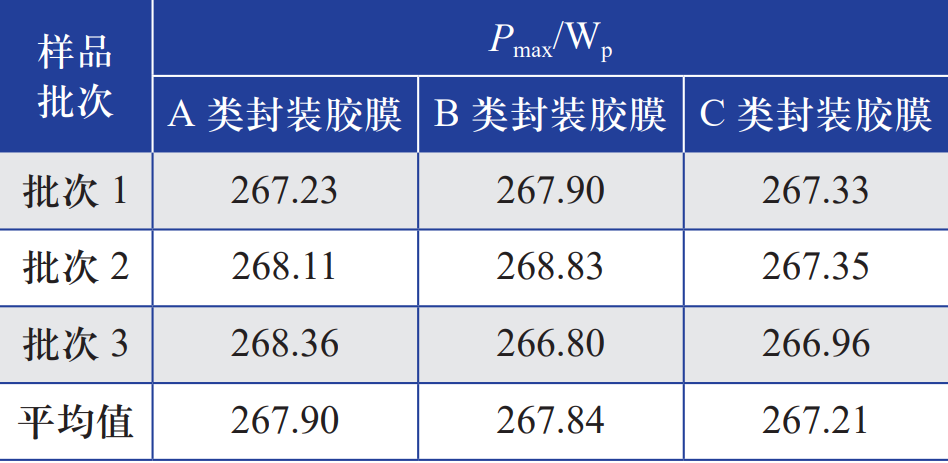
从表3可以看出:分别采用3类封装胶膜封装的光伏组件最大输出功率差异不大,最大输出功率平均值的差值小于1Wp,这说明这3种不同分子结构的封装胶膜对光伏组件输出功率差异的影响不大。
为加速光伏组件的抗PID性能测试,将上述制备的9块光伏组件样品按照IECTS62804-1-1—2020中的方法进行PID测试。
记录PID测试持续96h过程中各光伏组件漏电流的变化情况,不同类型封装胶膜封装的光伏组件漏电流的变化曲线如图2所示(以每类光伏组件3个批次的漏电流的平均值进行表征)。图中,正、负号代表电流方向,下同。
图2 PID测试中不同类型封装胶膜封装的光伏组件的漏电流变化曲线
从图2可以看出:PID测试中,采用A类封装胶膜(普通EVA)封装的光伏组件的漏电流绝对值明显高于采用B类封装胶膜(高阻助剂型EVA)或C类封装胶膜(POE)封装的光伏组件的漏电流绝对值,且采用POE封装的光伏组件的漏电流绝对值最低。
将光伏组件样品从实验箱取出,按照IEC60904-1-1—2017同时测试9块光伏组件样品的最大输出功率,然后根据式(1)计算PID测试后光伏组件的功率衰减率Pa,计算结果如表4所示。

式中:Pmax1为原始的光伏组件最大输出功率;Pmax2为PID测试后的光伏组件最大输出功率。
表4 PID测试后不同类型封装胶膜封装的光伏组件的功率衰减率
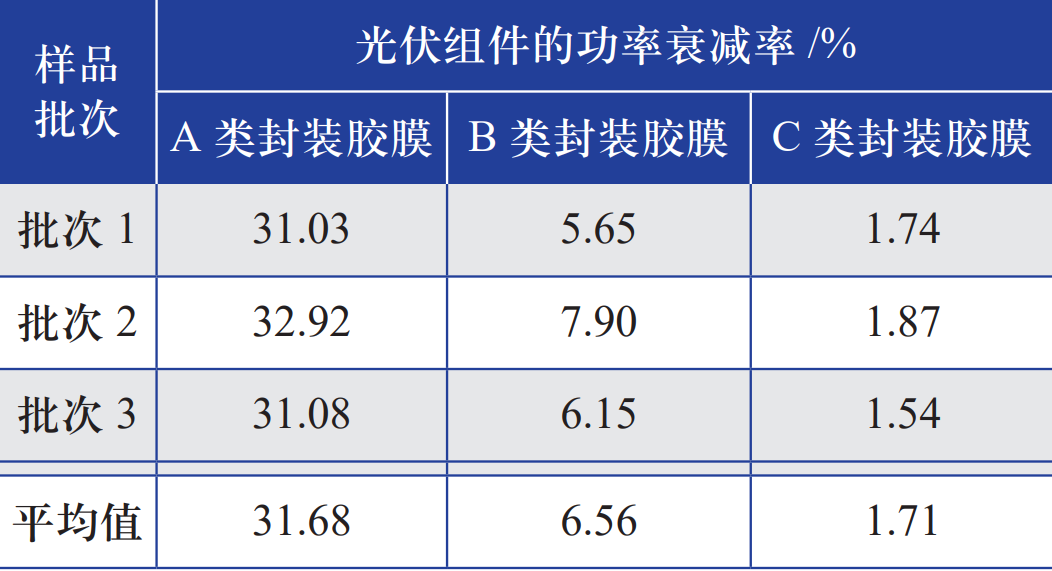
从表4可知:PID测试后,采用A类封装胶膜(普通EVA)封装的光伏组件的功率衰减率平均值达到了31.68%;采用B类封装胶膜(高阻助剂型EVA)封装的光伏组件的功率衰减率平均值为6.56%,说明高阻助剂型EVA对抑制光伏组件PID现象有一定效果,但并不能完全抑制PID现象的产生;而采用C类封装胶膜(POE)封装的光伏组件的功率衰减率最低,平均值仅为1.71%,说明POE有较明显的PID抑制效果。
为验证光伏组件PID修复过程的漏电流变化,对9块光伏组件样品进行实验室PID加速修复实验。
实验箱与前文PID测试的实验箱一致,电源电压为1000V,测试时间为96h。
记录PID修复过程中不同类型封装胶膜封装的光伏组件的漏电流变化情况(以每类光伏组件3个批次的漏电流的平均值进行表征),其变化曲线如图4所示。
图4 PID修复过程中不同类型封装胶膜封装的光伏组件的漏电流变化曲线
从图4可以看出:PID修复过程中,不同类型封装胶膜封装的光伏组件的漏电流从高到低的排序为:采用A类封装胶膜(普通EVA)封装的光伏组件>采用B类封装胶膜(高阻助剂型EVA)封装的光伏组件>采用C类封装胶膜(POE)封装的光伏组件。
结合图2的测试结果可以说明,无论是PID衰减过程中还是PID修复过程中,不同类型封装胶膜封装的光伏组件的漏电流绝对值从高到低的排序均为:采用普通EVA封装的光伏组件>采用高阻助剂型EVA封装的光伏组件>采用POE封装的光伏组件。
经过96h的PID修复后,按照IEC60904-1-1—2017中的要求再次测试光伏组件的最大输出功率,然后按照式(2)计算PID修复后光伏组件的功率变化率Pc,具体计算结果如表5所示。
式中:Pmax3为PID修复后的光伏组件最大输出功率。
表5 PID修复后不同类型封装胶膜封装的光伏组件的功率变化率
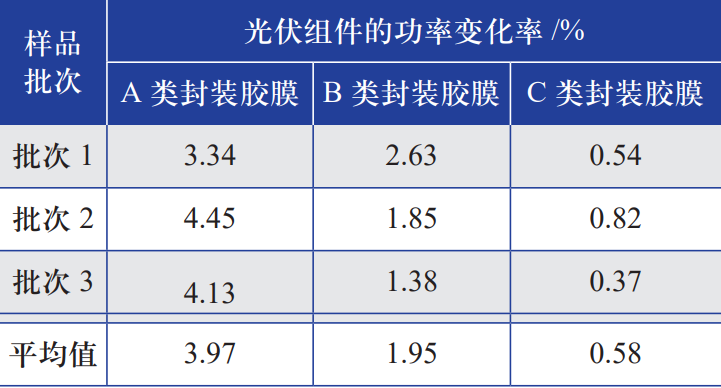
从表5可知:PID修复后,采用A类封装胶膜(普通EVA)封装的光伏组件的功率变化率平均值为3.97%,即修复率为31.68%–3.97%=27.71%;采用B类封装胶膜(高阻助剂型EVA)封装的光伏组件的功率修复率为6.56%–1.95%=4.61%;
采用C类封装胶膜(POE)封装的光伏组件的功率修复率为1.71%–0.58%=1.13%。
可以看出,采用普通EVA封装的光伏组件的PID值最大,对应的PID修复效果也较明显,说明光伏组件在高温高湿环境、组件边框与带电体之间外加正向电压的条件下,可实现大部分的功率修复。
根据前文实验结果对抑制光伏组件PID现象的机理进行分析。
当相对湿度超过40%时,空气中的水分通过光伏组件背板或硅胶渗透至玻璃表面,并与玻璃中的Na+进行离子交换产生Na2O或者Na2CO3;
另外,EVA中的酯键在遇到水后发生分解,产生可以自由移动的醋酸;可以自由移动的醋酸和玻璃表面析出的碱反应后,产生了可以自由移动的Na+。
Na+在外加电场的作用下向太阳电池表面移动并富集到减反射层,从而导致光伏组件PID现象的产生。因此,提高封装胶膜的体积电阻率,降低封装胶膜的醋酸析出,可有效抑制光伏组件PID现象的产生。
高阻助剂型EVA封装胶膜在普通EVA封装胶膜的基础上添加了抗PID助剂,该助剂为含乙氧基“”或含丙氧基“”的丙烯酸酯。
抗PID助剂采用以下一种或几种的混合物:乙氧化季戊四醇三丙烯酸酯、丙氧基化新戊二醇二丙烯酸酯、乙氧化三羟甲基丙烷三丙烯酸酯、乙氧化季戊四醇四丙烯酸酯、丙氧化甘油三丙烯酸酯、聚乙二醇二甲基丙烯酸酯、聚乙二醇二丙烯酸酯、聚丙二醇二甲基丙烯酸酯等。
由于该抗PID助剂主链为碳链,支链含有若干羟基的树脂结构,该结构与EVA树脂的水解产物结构相似,可以抑制EVA水解反应,有效减少EVA树脂的水解,从而可保证EVA膜的交联密度,提高封装胶膜的体积电阻率,达到抑制光伏组件PID现象产生的目的。
而POE封装胶膜与普通EVA封装胶膜的体积电阻率差异主要体现在粒子本身性能差异方面。
POE的分子结构如图5所示,主要为乙烯与α-烯烃共聚物,粒子为非极性树脂;而EVA的分子结构如图6所示,主要为乙烯-醋酸乙烯共聚物,由乙烯(E)和醋酸乙烯(VA)共聚而成,粒子为极性树脂。
POE和EVA的离子移动的能力存在较大差异,POE的离子运动较慢,因此POE的极化时间常数较长。
POE封装胶膜体积电阻率的提高,大幅减少了玻璃中Na+迁移到太阳电池表面的速度,从而达到了抑制光伏组件PID的效果。
本文通过实验验证和理论分析的方法,对不同分子结构的封装胶膜对光伏组件漏电流及抗PID的影响进行了实证研究,研究结果表明:
在相同实验条件(实验箱中环境温度85℃、相对湿度85%,外接-1000V直流电源,测试时间96h)下,采用不同分子结构封装胶膜封装的光伏组件表现出不同的抗PID性能。
POE封装胶膜的体积电阻率最高,对应的光伏组件抗PID性能最好;而普通EVA封装胶膜的体积电阻率低,对应的光伏组件无明显抗PID效果。
封装胶膜的体积电阻率越高,水蒸气透过率越低,对应的光伏组件的漏电流绝对值越低。
采用普通EVA封装胶膜的光伏组件在高温高湿条件下的功率衰减率平均值为31.68%,衰减速度快于其在常温条件(环境温度25℃、相对湿度50%)下的,高温高湿环境更易加速光伏组件PID现象,因而光伏组件应用于高温高湿环境中时,应优先选择POE封装胶膜。
由于光伏组件在电站中需要运行25年甚至更长时间,光伏组件PID现象对光伏电站的收益将造成长期影响。当前电站端光伏组件抗PID方案很多,提高光伏组件自身抗PID性能是最直接有效的方式。选择技术性能更好的光伏组件封装胶膜,对优化光伏组件抗PID性能有更高的品质保障。
来源:封装胶膜的体积电阻率对光伏组件抗PID性能的影响研究
原文始发于微信公众号(光伏产业通):封装胶膜的体积电阻率对光伏组件抗PID性能的影响