隐裂问题是指太阳能电池组件中的不良现象,可以影响组件性能,降低其使用寿命,有关人员应提高对此问题关注度以保证太阳能光伏产业发展不受影响,发挥太阳能电池组件最大价值。
工艺流程:电池分选-单串焊-叠层-层压-装框-清洗固化-测试-包装。
现阶段,有关人员将太阳能电池组件生产流程进行了细化,将其分为层压前、层压后以及包装前的 EL测试三大部分,然后还包括有一些小工序。在实际生产中,如果技术人员操作不规范将会出现隐裂问题。
而对存在隐裂问题的太阳能电池进行返修,不仅会增加生产成本,应用风险也会有所提高。
假设以已完成层压的组件为例,此工作阶段太阳能电池组件内部玻璃、EVA、电池片、背板等材料已经融合在一起,如果对隐裂位置进行更坏,则需要厂家支付多成本。
也就是说,在实际生产中,技术人员应严格遵守相关规定,不定期进行检查,降低隐裂问题发生概率,保证太阳能电池组件生产质量。
太阳能电池组件各个生产流程都可能引发隐裂问题发生。以某太阳能光伏企业组件生产线某班组工作情况为例,对其进行调查发现,在层压前阶段所产生隐裂情况,可以借助返工操作进行弥补。
基于此,在后续研究中,针对层压后各道工序所产生的隐裂问题进行了具体分析,并针对所总结原因提出了具体意见。对调查结果进行分析发现,因清装工序所引发的隐裂问题在所有隐裂问题中的占比高达 95.43%,即如何解决清装工序隐裂问题应成为技术人员重点关注内容。
清装工序主要作用是为完成层压的半成品组件安装铝边框与接线盒,对组件表面所黏附的 EVA溢胶以及组装时溢出的硅胶进行清理。
操作结束后,需要将其送入加湿固化装置等待硅胶固化,放置时间在10 h~12 h。
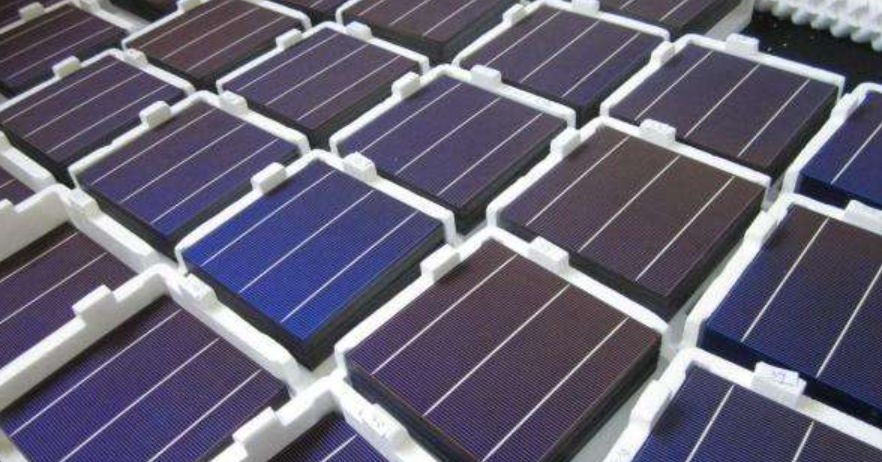
清装工序属于自动线流水作业,如果传输设备不平整或在运行过程中产生较大震动,则都可能引发隐裂问题。具体如下:
组框机顶升、翻转机吸盘不平整,在运行时产生较大冲击力。
在此次调查过程中,该班组共生产了540 块组件,进行了四次 EL 测试,分别是组框前、组框后、翻转机翻转前以及翻转后。
对调查结果进行分析发现,组框前与组框后共有 33 块太阳能电池组件发生隐裂问题,在总数中的占比为 6.11%;翻转机翻转前以及翻转后共有 28 块太阳能电池组件发生隐裂问题,在总数中的占比为 5.19%。在实际生产中,由于组框机顶升与翻转机吸盘一直处于使用状态,因此会产生不同程度磨损,以致于出现组框机顶升、翻转机吸盘不平整问题。
如果发生此类问题,则在后续生产时,对组件所造成的冲击力也存在一定差异,以至于组件平面发生形变,出现隐裂问题。
对翻转机后方单元组件进行分析可知,相关传输单元并未处于同一平面,以至于在流水线生产过程中组件会出现下坠情况,导致组件玻璃面与传输轨道线体发生碰撞,进而产生形变。
借助随机抽取方法选择 100 块组件进行测试发现,经过 EL 测试后,共新增隐裂组件 3 块,隐裂问题发生概率约为 3%。
托盘组件数量较多。将所生产组件分成若干份放置在托盘中,然后开展 EL 测试,测试结果表明,当托盘组件数量超过 20 块时,隐裂问题发生概率明显提高。
为解决上述问题,在实际工作中,技术人员可以借助以下措施降低隐裂问题发生概率:
借助水平仪等设备对组框机顶升进行校准,使用四角误差法组成拼装面积,提高组件与顶升二者的接触面积,降低组件所承担振动,降低隐裂发生概率。
借助水平仪等设备对组框机顶升进行校准,调整固定吸盘所用螺母的位置,然后在其中增加一块玻璃,调整吸附气压使其可以刚好完成玻璃吸附,降低隐裂发生概率。
对线体传输单元支撑脚进行优化,借助水平仪等设备对传输轨道进行校准,提高组件传输过程稳定性,降低组件所承担震动,降低组件磕碰概率,降低隐裂发生概率。
为验证前文所讲述内容,笔者借助工程实例进行了验证。所选择工程实例为在山地建设的集中式光伏电站,共拥有场区方阵 20 个,所选择逆变器为集中式逆变器,总装机容量 20 MWp,拥有太阳能电池组件79 000 块,每 21 块电池组件组成一个电池组,具体排列方式为 3 行×7 列,表 1 为太阳能电池组件发电参数实测表。
表 1 太阳能电池组件发电参数实测结果表
隐裂是指太阳能电池组件在完成封装后,由于所受机械力或热应力较大,导致电池电源出现肉眼无法发现的细微裂纹。隐裂的存在会对太阳能电池组件性能造成影响。限制电池组件性能。
太阳能电池组件电流传输原理为:由细栅线完成电流收集,然后将其传递给主栅线路,在借助互联条将各个电池组件正负极主栅线路连接在一起,为光伏组件提供电能。
太阳能电池组件电流大小与电池片发电面积二者而反比关系,如果存在隐裂问题,则可能会引发细栅线断裂问题,导致所产生电流无法及时传递给主栅线,导致电池片无法发挥自身实际作用。
当太阳能电池组件内部光伏板存在隐裂问题,则线路整体电能供应效果由隐裂电池片决定。如果电池片失效面积较大,无法形成负载,则会引发短路情况,具体情况如图 1 所示。
除此之外,在裂纹截面的晶硅残渣会搭接在一起,导致出现局部短路问题,导致主电路漏电,进而对其输出功率造成影响。
并且,伴随机械载荷不断增加,电池组件隐裂程度也将持续增加,进而会引发开路性的破损。当隐裂情况增加到一定程度时,还会引发热斑效应,导致隐裂电池片局部温度不断提高,导致组件封装材料老化速度不断提高,对太阳能电池组件电流输出功能造成影响,降低组件使用寿命。
对太阳能电池组件隐裂问题进行收集可知,可以将其细化为六种,分别是树状裂纹、综合型裂纹、+45°/-45°斜裂纹、平行于栅线、垂直于栅线、贯穿整个电池片的裂纹,具体情况如图 2 所示。
不同裂纹形状会对太阳能电池组件造成不一样的影响。对晶硅电池板结构进行分析可知:垂直于主栅线的细栅线主要功能为电流收集,因此当太阳能电池组件出现平行于主栅线、垂直于细栅线的裂纹,则会对太阳能电池组件电流收集能力造成影响,导致电池片部分功能受损。
以德国 ISFH 研究所研究成果为例:50%的电池片受损与平行于主栅线的隐裂有关,斜裂纹、树状裂纹、综合性裂纹影响都在 14%~20%,由垂直于主栅线的隐裂产生衰退的电池片只有 1%。
由于隐裂较小,工作人员无法借助肉眼进行识别,因此在实际检测过程中,工作人员需要借助相关仪器设备。
对现阶段太阳能电池组件隐裂检查手段进行收集可知,除前文所提到的 EL 测试外,还有电子散斑干涉法、光致发光(PL)测试、超声波谐振探测法等方法。在实际工作中,工作人员应结合实际情况进行选择。
结合相关于要求对太阳能电池组件生产原料进行检查,结合实际情况控制互联通厚、硬度以及可焊性。
严格遵守相关规定,确保工艺参数符合生产标准、提高对生产过程检试验管理关注度,对生产设备进行优化,提高生产线工人操作规范性,具体措施如下:
层压前重点控制焊接质量,电池片需经过充分预热后再实施焊接,焊接时避免虚焊、过焊和焊带偏移,避免按压电池片。
提高层压前 EL 检查重视程度,尽量在层压前完成隐裂返修,避免之后的操作导致隐裂扩大。
层压后的组件应充分降温后才能进行削边,宜采用玻璃面向下的方式削边和装框,装框前的层压件应避免翻转和人工搬运。
确保削边和预组框等工作台面积足够大,在工作中,组件处于中间位置,组件边缘与台面边缘之间的距离不得低于 200 mm。
借助钢架托盘或双层木托盘来协调所存放组件关系,借助叉车进行转运时,货叉必须完全穿过托盘。
通过本文论述可知,隐裂问题是影响太阳能光伏企业发展、限制太阳能电池组件发挥自身价值的关键问题。
因此在实际操作中,除使用本文所讲述内容提高清装工序工作质量,降低隐裂问题发生概率外,还应用通过工作人员培训,提高实际工作质量,提高操作规范性,以降低隐裂问题发生概率,挖掘太阳能光伏电池组件潜能。
原文始发于微信公众号(光伏产业通):太阳能电池组件隐裂在清装工序中的控制